The most remarkable thing about Kevin and Lukas Czinger is not the fact that they have built a hypercar – one of the fastest and most remarkable hypercars the world has ever seen and one capable of giving established players, like the McLaren P1, a solid kicking – but why, and how, they’ve done so.
Kevin – an inventor and entrepreneur who was once a United States federal prosecutor who worked with Rudy Giuliani – and his son Lukas built the Czinger 21C to prove a point: that cars could be constructed in a more environmentally friendly way using AI to perfect parts before they are made, and then 3D printing as many of those pieces as possible.
They could, of course, have built a small, city-friendly electric vehicle (EV) to do that, but the fact is they also love cars and, quite possibly, showing off a bit. And when you want to get the attention, and the investment, of the world’s largest car companies, showing them up is definitely one way to do it.
The Czinger 21C – designed to resemble a jet fighter and taking no small amount of inspiration from the famous Blackbird spy plane, with the passenger sitting behind the driver – definitely shows the established experts how it’s done.
Reinventing body construction wasn’t enough for the Czinger boys and they also designed their own powertrain – a twin-turbo, 2.88-liter V8, which they claim is “the most power dense” production engine in the world – and sent the blueprints off to a small company in New Zealand, which built the block for them.
That engine is combined with a hyper hybrid setup involving two electric motors on the front axle, which means that, much like the McLaren P1, you’ve got an electric car and an internal-combustion one stuck together – and that means absurd amounts of power.
Proving a Point
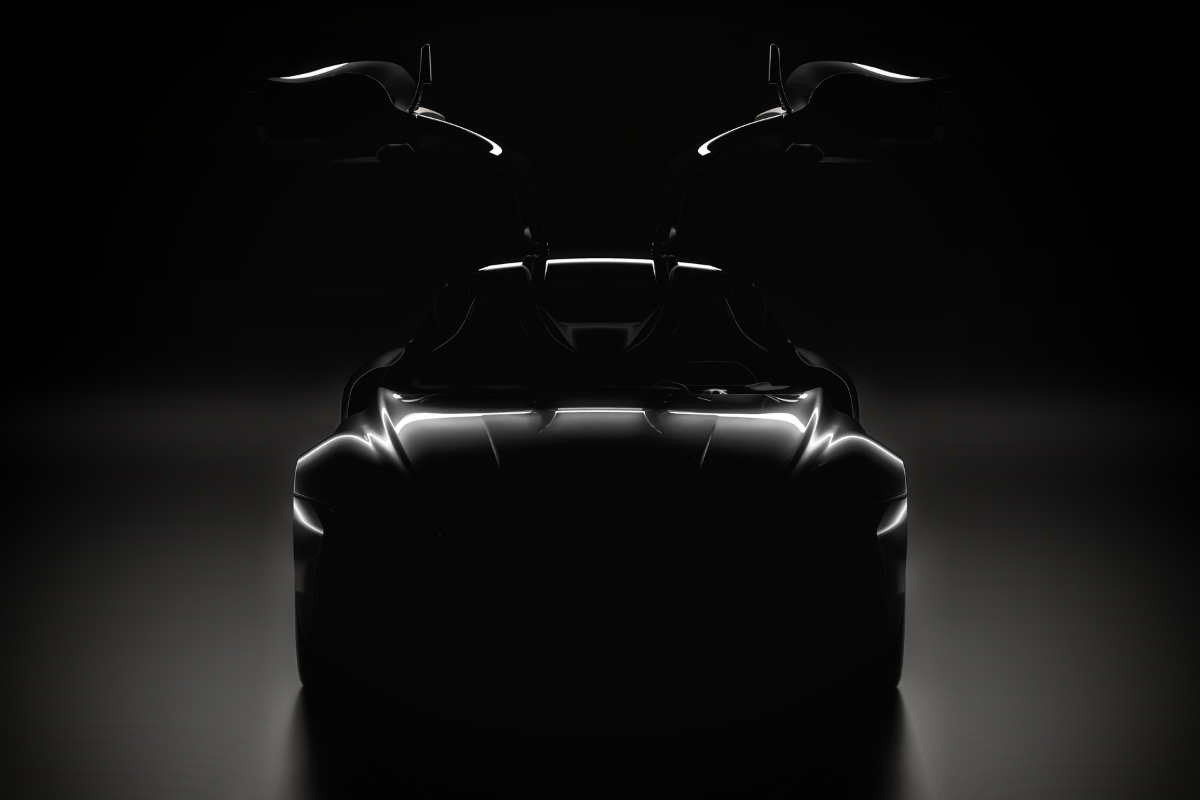
Czinger claims its 21C is putting out 932 kilowatts and 1,439 newton-meters in a super-light vehicle made of titanium, carbon fiber and aluminum that weighs just 1,250 kilograms.
This means it can hit 100 kilometers an hour in under two seconds, or 300 kilometers an hour in just 15. It recently set a sizzling lap time at the Circuit of the Americas in Austin, Texas, that was a whopping 6.5 seconds faster than the P1, which, as Kevin points out, “is an eternity in a performance car”.
There’s a YouTube video of this lap being set, and I would suggest that you should not watch it if you have any kind of heart trouble.
Czinger has proven that its radical processes can produce something radically fast then, but it will build only 80 examples of the 21C, perhaps because there aren’t that many people in the world who could drive the damn thing.
A four-seater Hyper GT, using the same bonkers power plant, has recently been unveiled and will be ‘more affordable’ than the 21C, which is a relative term because that car is priced at US$2 million.
More models, as many as half a dozen, are on the way, but that’s not where the growth is for Czinger, which has already signed up Aston Martin and is 3D printing frames for it, and Kevin says several other giant brands have also shown interest, thanks to the deafening buzz created by the 21C.
“The thing that, to me, defines what being a human being is, at the apex, is expressing that creativity in actual physical objects in the world. And so if you have these tools, you want to show how that can be done,” Kevin explains to The CEO Magazine.
“It’s been proven possible in this technology, and that’s how we got other car companies to adopt it. They couldn’t afford not to.”
Starting Anew
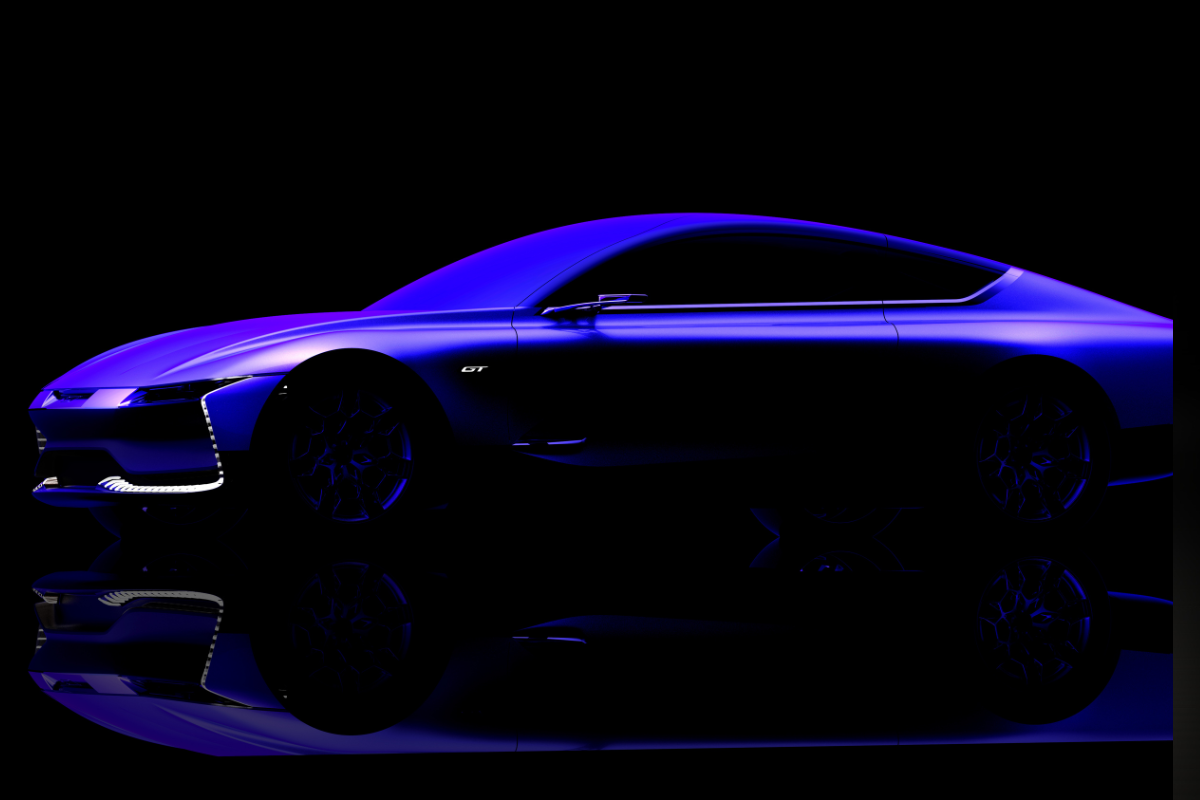
The inspiration to turn the world of car manufacturing on its roof came to Kevin when he was running an EV company and touring an enormous, 90,000-square-meter-plus EV battery factory in China, back in the nascent days of EVs in 2008.
“So environmentally, I thought I was kind of saving the world with EV batteries, until I did the analysis of the emissions from manufacturing them, and realized that China was using almost exclusively coal-fired power generation for its factories,” he recalls.
“And I’m standing there thinking … manufacturing is really the driver of emissions. And from an environmental standpoint, we needed to move from these analog, capital-intensive material and energy-inefficient ways of manufacturing things – stamping, casting and so on – to fully optimized digital manufacturing.
“So I sat down and said, ‘I’m gonna start with a clean sheet of paper and create that system.’”
The result was Divergent Technologies, a technology development company working in digital manufacturing. Czinger is largely owned by Divergent and is the ‘product’ arm of the business, proving its wares in spectacular fashion.
Lukas explains that the Czinger setup doesn’t look like a car factory. It’s a climate-controlled room with printer models and robots, creating parts that are digitally designed using AI. “They’re literally perfectly optimized – no human engineers can do in three dimensions what the AI can,” he says.
“Usually it would take months of engineering, but it’s compressed really into hours of high-performance computer simulation time and then, once we have that design, you actually send that to our 3D printers, and then to the robots to put those parts together.
“We print using the aluminum alloys that we’ve designed, so there’s no rare-earth minerals, no welding, and there’s no complicated process with melting them so we can quickly re-optimize them and turn them back into a standard, 3D-printable powder and print new components.”
Transforming Production
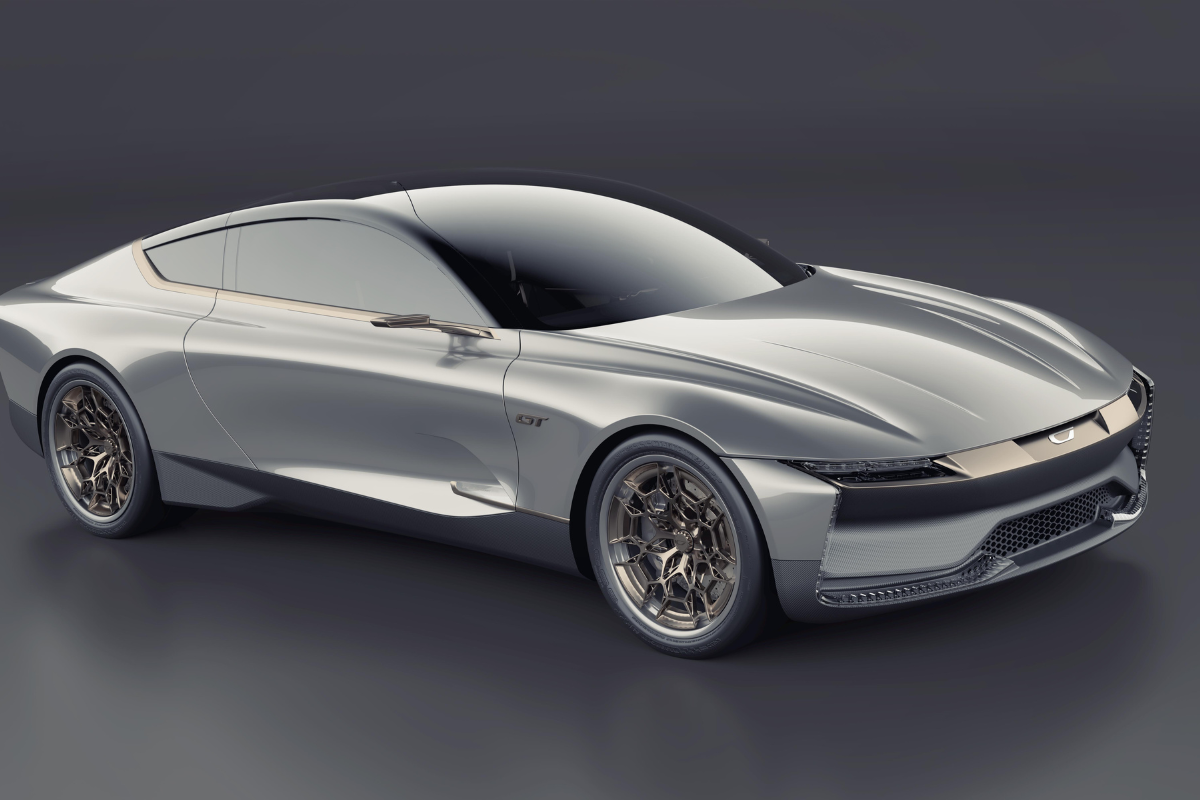
Each printer can produce one kilogram of parts per hour so, with dozens running at once, Lukas says the frame for a single Czinger car, containing 21 parts, takes just seven minutes. Working at such high speed uses less energy, of course, but it also means it’s easily scalable to mass production.
The way the design process works also focuses on keeping the parts, and thus the whole car, as light as possible, which means using fewer materials.
“If you want to be sustainable, if you want to decrease CO2 emissions per annum, you need to use a lot less material, and we’re able to, off the bat, use 30 to 40 percent less material,” Lukas enthuses.
“What Kevin and I are after is not just having an impact on the fastest cars and the highest price point cars in the world, but fundamentally rethinking and implementing a new manufacturing system that’s going to address all complex structures – automotive at high volumes, aerospace, defense and any complicated metal structure. That’s a market that we’d like to transform for the better.”
Sure, super-fast hypercars are exciting, but a new form of manufacturing that’s less material- and energy-intensive and far more recyclable? That’s actually the most interesting part of the Czinger story.