It was 1992; the word “futuristic” still conjured up fantastical images of flying cars and time travel that couldn’t seem to happen without lightning bolts à la Back to the Future. Somewhere in Germany, in his parents’ garage, a young Thomas Hähn was hard at work. Just like Doc in Back to the Future, he was building something futuristic.
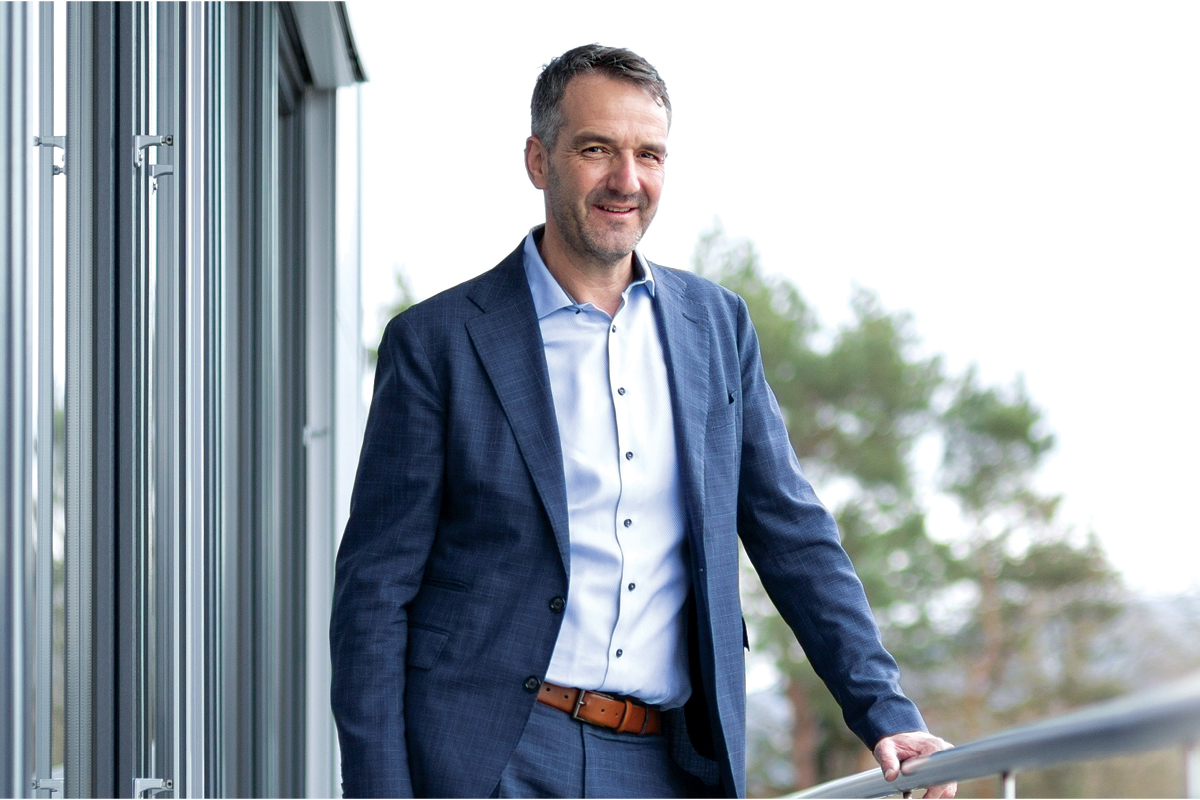
“When I was still a student, I worked at Boge Rubber & Plastics, where I invented an automatic loading system for rubber injection molding,” he recalls. “The company went into a merger process just as I finished my studies, so couldn’t offer me a job. I couldn’t stop thinking about my vision, though, so I continued to work on its development in my parents’ garage.”
An automated solution for rubber presses may not offer the same imaginative possibilities as a flying time-travelling car, but it was more realistic. Thomas didn’t know it at that time but the creation would come to shape his career.
By a stroke of serendipity, Thomas met Brad Corbett a few years after putting his automation device out on the market. Better known as the principal owner of the Texas Rangers baseball team, Brad had made his fortune earlier in life manufacturing plastic pipes. “He was first interested in my products as a customer,” says Thomas. “Then he decided to help us enter the US market by offering a joint venture. That was how we took our first step towards becoming a company with a global presence, seven years after I began building my automated system.”
The joint venture saw the founding of Hahn Automation. Fast forward to 2014, and it hit another milestone. “Jürgen Wild, CEO of RAG-Stiftung investment company, expressed interest in investing in our product portfolio. We incorporated the Hahn Group and have grown 400% over the past five years,” Thomas enthuses.
Today, Hahn Group has 11 subsidiaries, some 1,400 employees across 24 locations and a turnover three times what it was in 2014. Thirty to 40% of its business has to do with medical devices, and the segment is one of its biggest focuses.
As one can imagine, industrial automation has changed drastically since Thomas began tinkering with it in 1992. Ensuring that Hahn Group keeps up with the industry’s constant changes has always been his priority. And the current preoccupation of the industry? Digitalisation.
“The biggest need for digital products right now is in manufacturing sites,” Thomas explains. “We can now collect data from the machines, both during the production process and for the end products. Evaluation of this data mix allows us to improve our robotic solutions, leading to a more reliable and faster, as well as cost- and resource-efficient, production process.”
Allowing Hahn Group’s customers to take full advantage of its digital solutions is its EVE smart services product. This interface, which won the 2019 Innovation Award of the Ministry of Economics Rhineland-Palatinate, provides easy monitoring of the manufacturing process. Every production machine and robotic cell can be connected to the software and their statuses monitored from a PC, smartphone or tablet. The interface even boasts augmented reality technology that is made possible with smart glasses.
When a customer calls a Hahn Group service technician while wearing the glasses, the technician can see exactly what the customer sees, eliminating the need to constantly turn a phone screen around or engage in longwinded descriptions about what is happening on-site.
“Digitalisation is still new to our industry, so we are working with our customers to understand their concerns in bringing digital products into their production plants. We want to offer only products and services that are valuable to our customers,” Thomas emphasises.
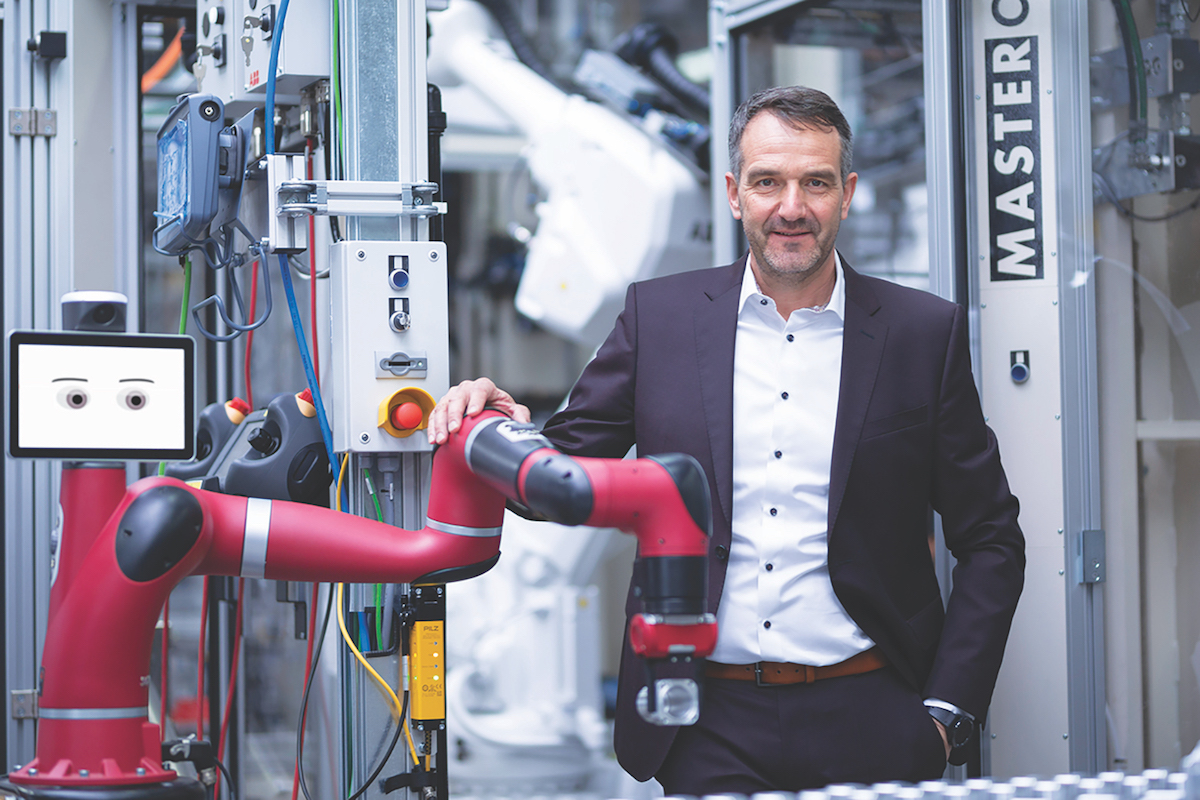
In addition to working with customers, digitalisation also results in stronger supplier relationships. For example, Hahn Group has a 25-year partnership with Bosch Rexroth Group that continues to strengthen as they work together towards future growth in the areas of automation and Industry 4.0 applications.
Despite having made a career out of robots and automated machinery, he believes there are some areas of production where the human touch will remain indispensable. “The biggest challenge is in understanding and accepting that artificial intelligence in the automation industry will turn machines into learning machines,” says Thomas. “But the industry will continue to require human decision-making when it comes to complex problems.
“It’s human skills that create and continuously improve robotics and automation solutions.”
“It’s human skills that create and continuously improve robotics and automation solutions. Therefore, human intelligence will always be valuable, even in an increasingly automated world.”
Proudly supported by:
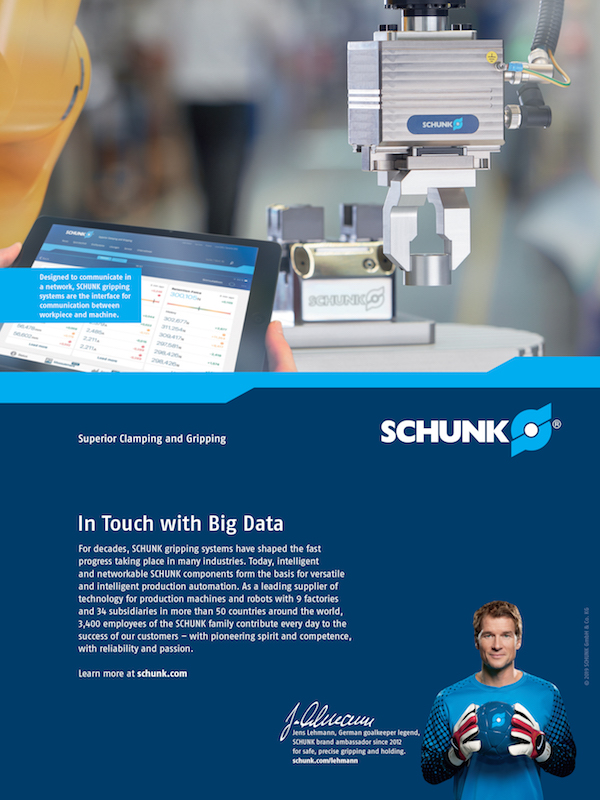