Pang Chong Yong has spent nearly half of his life in the pursuit of the very best in bus body technology. However, his first exposure to buses was even earlier, and related to a very different feature. In 1983, he was a partner in Hotoh Bus & Car Air-Conditioning in Malaysia. The air-conditioning industry at the time was in the early stages of a big boom.
“A lot of used cars, trucks and buses still had no air-conditioning service. Back then, it was only a feature for luxury cars,” Chong Yong recalls. “There were a lot of air-conditioners coming from Japan, from Germany. I had a chance to train myself in service and repair, and we just grew from there.”
Pang Chong Yong finds the latest in bus body technology
He continued in the car and bus air-conditioning business for a number of years. It wasn’t until 1989 that he decided to switch his focus to bus bodies instead, co-founding Gemilang International with his cousin, Phang Sun Wah. Chong Yong took on the CEO position and Sun Wah became the chairman. They realised that the bus bodies being manufactured were very basic and lacking in quality and technological innovation.
“Chassis were also very basic; they were normally just a quick conversion job from trucks now used on buses. They were not tailor-made,” Chong Yong says. Over time, Chong Yong did some research overseas, trying to bring in the latest technology in the market to Malaysia, and designed and built an aluminium alloy body made specifically for buses.
“An aluminium body comes at a slight premium compared with bodies made from steel, but it’s a strong, lightweight solution and could last for 20 years with no corrosion,” he remarks.
“The steel body, on the other hand, after three to four years, rusts and corrodes, weakening the structural frame and compromising the body’s integrity. Also, you can only recycle 10 to 20% of a steel body because of the corrosion, whereas with aluminium you can recycle between 70% and 80% of the body.”
Gemilang capitalises on the aluminium trend
Gemilang has been up and running for more than 28 years, longer than the estimated durability of its aluminium alloy bus bodies, and boasts a product range that caters for single deck, articulated and, most recently, double-decker buses.
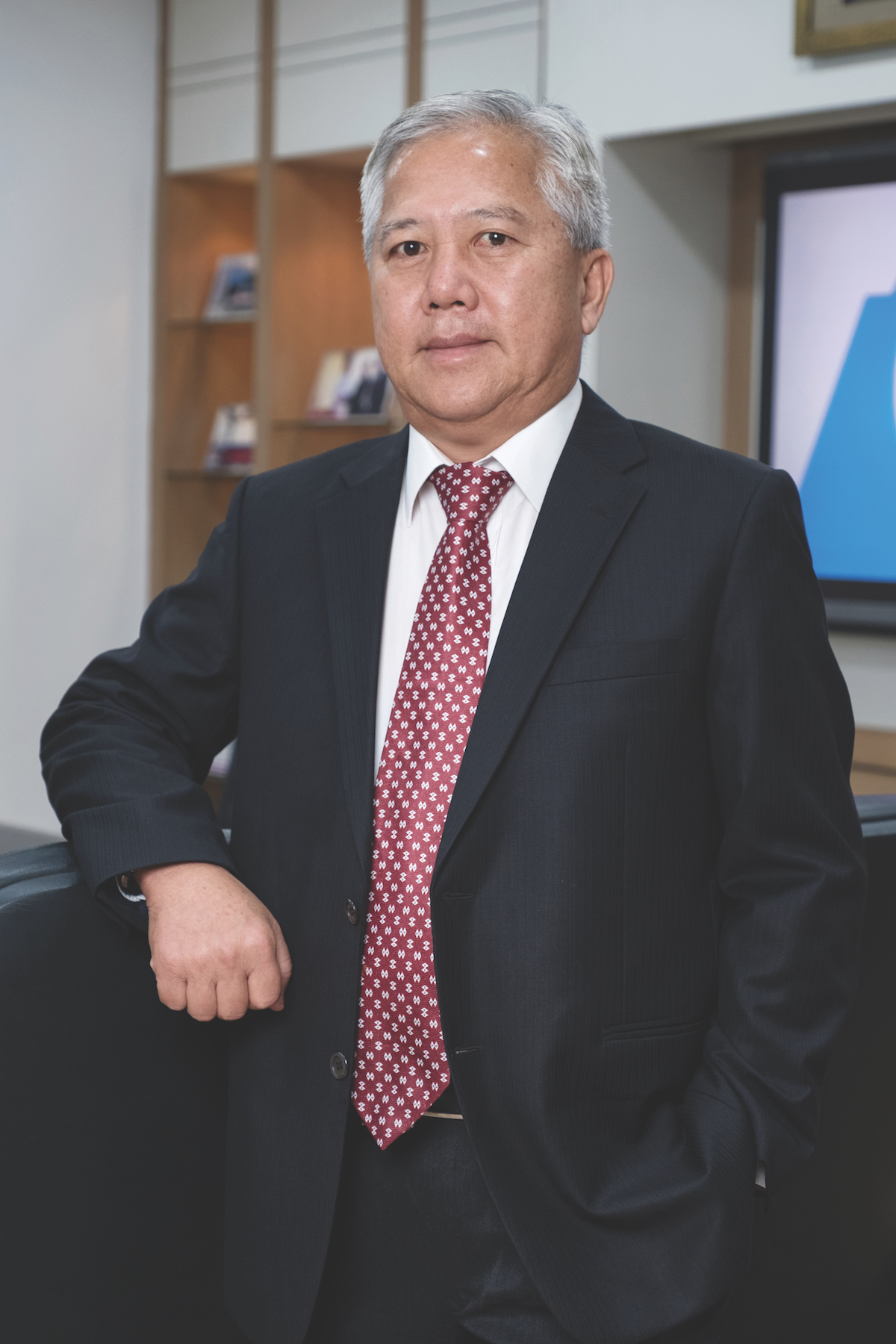
As well as the primary markets in Malaysia and Singapore, it also exports to Mainland China, Hong Kong, Australia, New Zealand and Uzbekistan, among others. In the year ending 31 October 2016, Gemilang recorded a revenue of US$48.69 million, an 18.6% increase from the previous year.
As further evidence of the aluminium trend, 85.2% of that revenue came from aluminium products compared with 10.4% from steel products. The disparity is even more pronounced over the first six months ending 30 April 2017, according to Gemilang’s Interim Report, with 90.1% of revenue from aluminium and 4% from steel.
Chong Yong wants to teach people about the importance the bus body has on a vehicle’s overall integrity, particularly to those who may harbour what he believes could be damaging misconceptions, especially as more countries move to electric buses in order to meet global environmental targets.
One such misconception is that improvements to the body are minimal, even cosmetic, compared with other features such as the engine or safety features. Chong Yong points out that it doesn’t matter how many improvements are made to the other areas of a bus; if the body is too heavy, those improvements are effectively rendered meaningless.
“If a bus is very heavy, it needs a lot more battery to run than if it was built on a full aluminium alloy chassis. The vehicle would be lighter by one or two tonnes,” explains Chong Yong. “For the efficiencies of electric buses to be realised, we need to pursue every effort to reduce the weight from the body, especially with our aluminium body structure and design. It will lead to more efficient use of the battery and will lengthen the durability of the bus.”
New technology and new ideas
The other common misconception, according to Chong Yong, is the view that bus body improvements are not high-tech. “The reduction of weight in vehicles can be a very big job to undertake. There is a lot of high technology involved,” he says. “For example, a Hymer van has a chassis that is like a truck base. It’s designed in Europe. We use our aluminium superstructure that is seamlessly integrated with the chassis, creating a semi-to-full monocoque design.” With all this pressure to keep up to date with the latest technological advances, Chong Yong believes it is very important that he interacts closely with staff on the ground.
“Especially because we are bringing in new technology and new ideas from overseas, we need to work very closely with our staff and explain it to them,” he says. “Quite often, we have to send our supervisors overseas for training as well.”
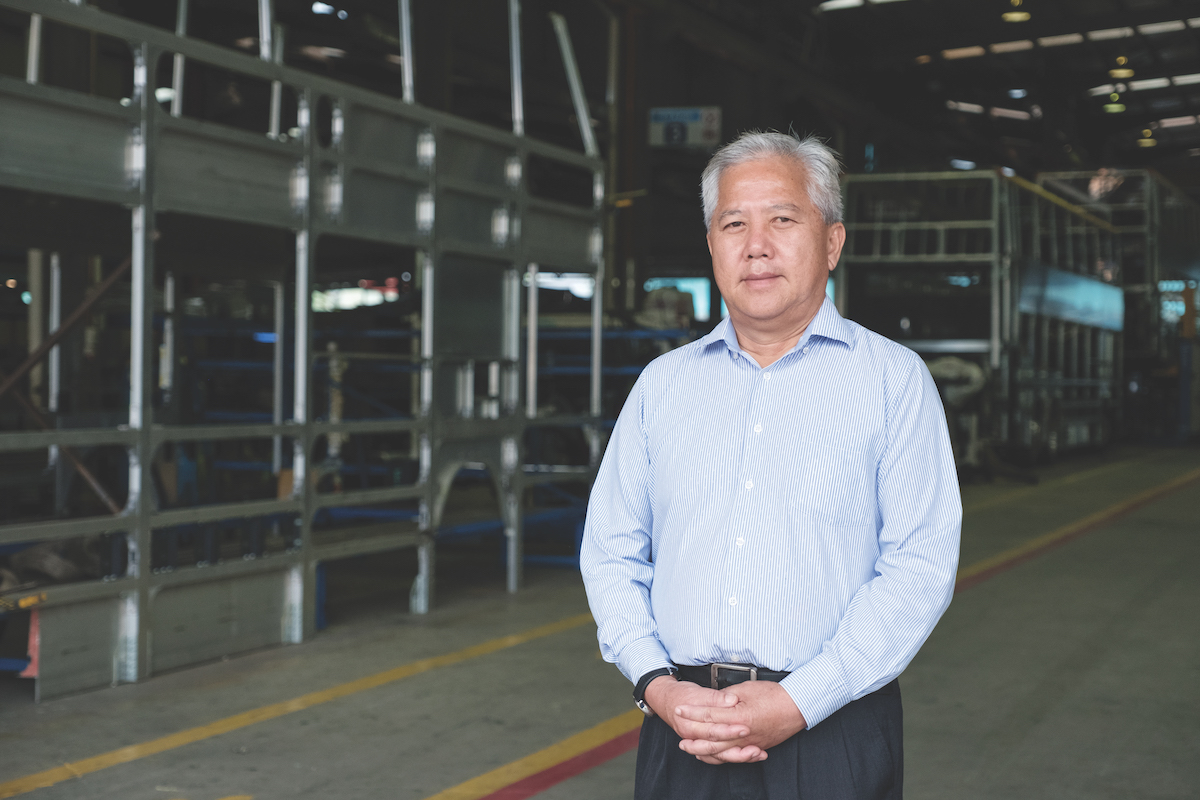
Our work on the double-decker light body is something I’ve found very satisfying.
Most recently, Chong Yong says, the company has been working on designing bodies for double-decker buses. The overwhelmingly positive response it has received over the past two to three years while promoting the double-decker product is something from which he derives immense pride.
“Our work on the double-decker light body is something I’ve found very satisfying; I view it as a major achievement for our company,” he says. “It is now one of our main products.”
Despite possessing deep technical knowledge and know-how, the ultimate goal for Gemilang remains a simple one – to be one of Asia’s leading business manufacturing solution providers. It wants to open up new business opportunities, especially in China, where it sees the biggest growth potential.
Improving competitiveness in Asia
In its 2016 annual report, Gemilang signalled intentions to set up an office and a manufacturing facility in China, noting demand for buses is expected to increase by an average of 9% per annum from 2016 to 2020. General demand for electric buses is also expected to increase. “In China, everything is becoming electric. That includes cars and buses,” Chong Yong adds.
Further, he is looking to expand Gemilang’s export base beyond its existing markets and into the Middle East and Central Asia, Uzbekistan being one of its current export markets. He says the opportunity in the Central Asian nation came about through an existing relationship with a European chassis supplier that also had an interest and investment in the area.
“I believe they are also in a hurry to come up with a hybrid electric system. Of course, if they come up with those systems, we will be perfectly placed with our light aluminium solution,” he says.
But most importantly, Chong Yong hopes the business will be able to solidify relationships with its existing chassis manufacturers and create new ones. Without them, there would be no market for bus bodies and, in turn, no Gemilang. “We need to work closely with our chassis suppliers, including Mercedes and Hyundai,” he says. “Over the years, I think our products have become more widely recognised in terms of price and quality. We hope to keep improving on our competitiveness in Asia.”