Alongside India’s population growth and economic renaissance over the past half century, there are innumerable stories of entrepreneurs stepping up to meet the challenges of the era.
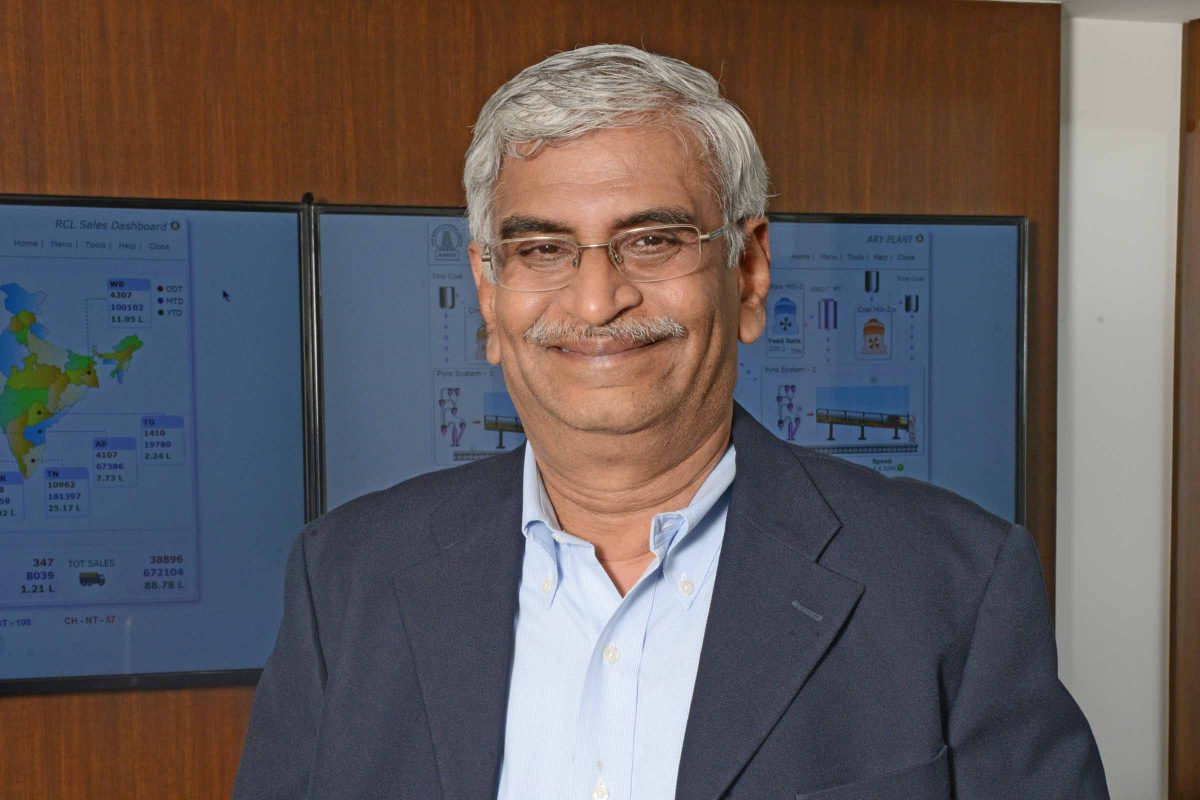
One such story is worth telling. Back in 1961, an entrepreneur named PAC Ramasamy Raja started a small cement factory in Madras (now Chennai), fittingly called Madras Cements, but unfortunately died soon after in 1962 and never saw his dream realised.
His son, PR Ramasubrahmaneya Rajha, was then appointed Managing Director of the company in 1962 and took it on a journey that met his father’s ambitions and much more besides, holding that position until 2017.
The company, now called The Ramco Cements, is the flagship company of Ramco Group, headquartered in Chennai, South India. From very humble origins, the company is now a multi-tiered vertical operation that caters to southern India’s burgeoning construction and infrastructure demands.
Its primary product is Portland cement,which it manufactures in eight state-of-the art production facilities, making The Ramco Cements the fifth largest cement producer in the country. The most popular cement brand in South India is undoubtedly Ramco Supergrade, but it also manufactures ready-mix concrete and dry mortar products.
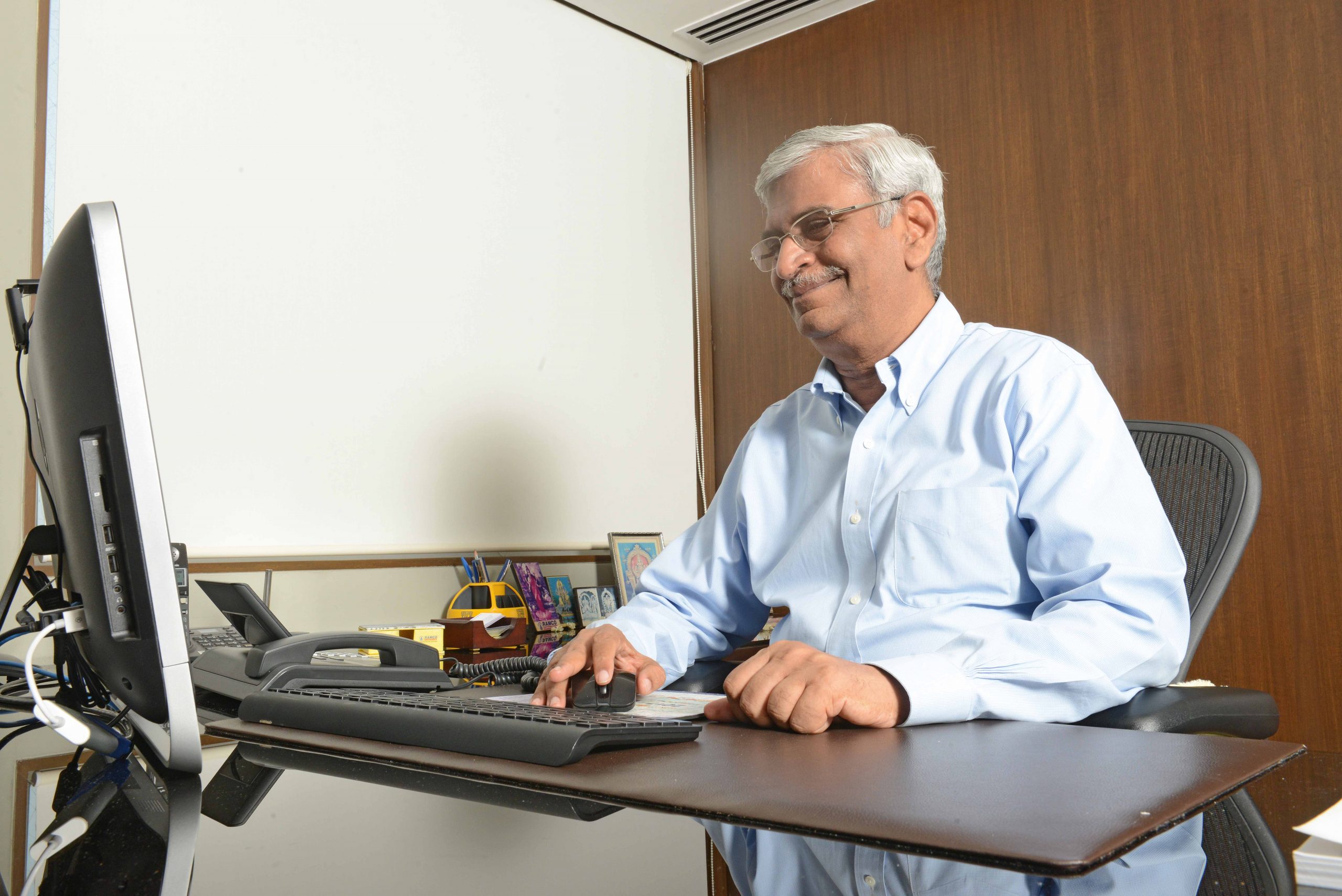
The company operates integrated cement plants in Ramasamy Raja Nagar, Alathiyur and Ariyalur in Tamil Nadu, Jayanthipuram in Andhra Pradesh and in Mathodu, Karnataka. It also has four satellite grinding units, located at Uthiramerur and Valapady in Tamil Nadu, Kolaghat in West Bengal and Visakhapatnam in Andhra Pradesh, with a total grinding capacity of around four million tonnes per annum.
The company’s steady growth included building a ready-mix concrete facility in South Chennai in 1999 and a dry mortar plant in 2002, as well as a packing terminal in Kumarapuram, Tamil Nadu. It also ventured into other business opportunities, including the acquisition of Gokul Cements in Mathodu in 2000, whose capacity is 290,000 tonnes per annum.
It has invested heavily in industrial research and its well-regarded research facility, the Ramco Research & Development Centre (RRDC), is located in Chennai.
India is now the fourth-largest producer of wind power in the world and, predicting the transformation of the energy industry early, Ramco established the Muppandal Wind Farm in 1993 – India’s largest onshore wind farm.
We follow our founder’s strong belief in ethical values, leadership qualities and motivation to form a committed team.
Its early operational success encouraged the company to build wind farms in Poolavadi in 1995, Uthumalai in 2005 and a six-megawatt wind farm in Karnataka in 2006 to supply the energy needs of its Mathodu cement plant. The company’s total energy production capacity now reaches nearly 165 megawatts.
These diverse operations have a total employee count of more than 3,300, all of whom have their own stories to tell. One employee in particular, The Ramco Cements CEO AV Dharmakrishnan (or AVD as he is known), has witnessed that long history of development, expansion and market dominance. He joined the company as a chartered accountant in 1982, when it was still known as Madras Cements.
AVD’s unique combination of an interest in technology and financial expertise means he has served the company well in every area of its operations, including staff recruitment, project development, plant and equipment selection and installation, and operational streamlining for greater efficiencies.
He has also served as a NonExecutive Director at other Ramco Group companies such as textile manufacturer Rajapalayam Mills and enterprise software company Ramco Systems. “I joined The Ramco Cements as accounts officer and within four years I was promoted to CFO of the company,” AVD recalls.
Ramco in the wind
The Ramco Cements opened its first wind farm at Muppandal in 1993, and in 1995, it installed an additional 69 windmills at Poolavadi. In 2019, its total installed windmill capacity with 235 individual units is about 165 megawatts.
“With a lot of designation changes and some functions being added to my responsibilities, I effectively became almost like a CEO from about 2000.
“When I joined the company, it had a very small capacity of just half a million tonnes. Today, the production capacity of The Ramco Cements is about 12 million tonnes. We have plans to increase that capacity to 20 million tonnes – they are being implemented and should be completed about the middle of this year. Once these expansion projects are finalised, we have plans to go to the next level of expansion, to 25 or 30 million tonnes.”
The right cement
Different project types require different types of cement to ensure structural integrity and meet legislative demands. Ramco has driven Indian research into the subject at the RRDC, where it conducts tests on cement and concrete, and its ability to contribute to sustainable development.
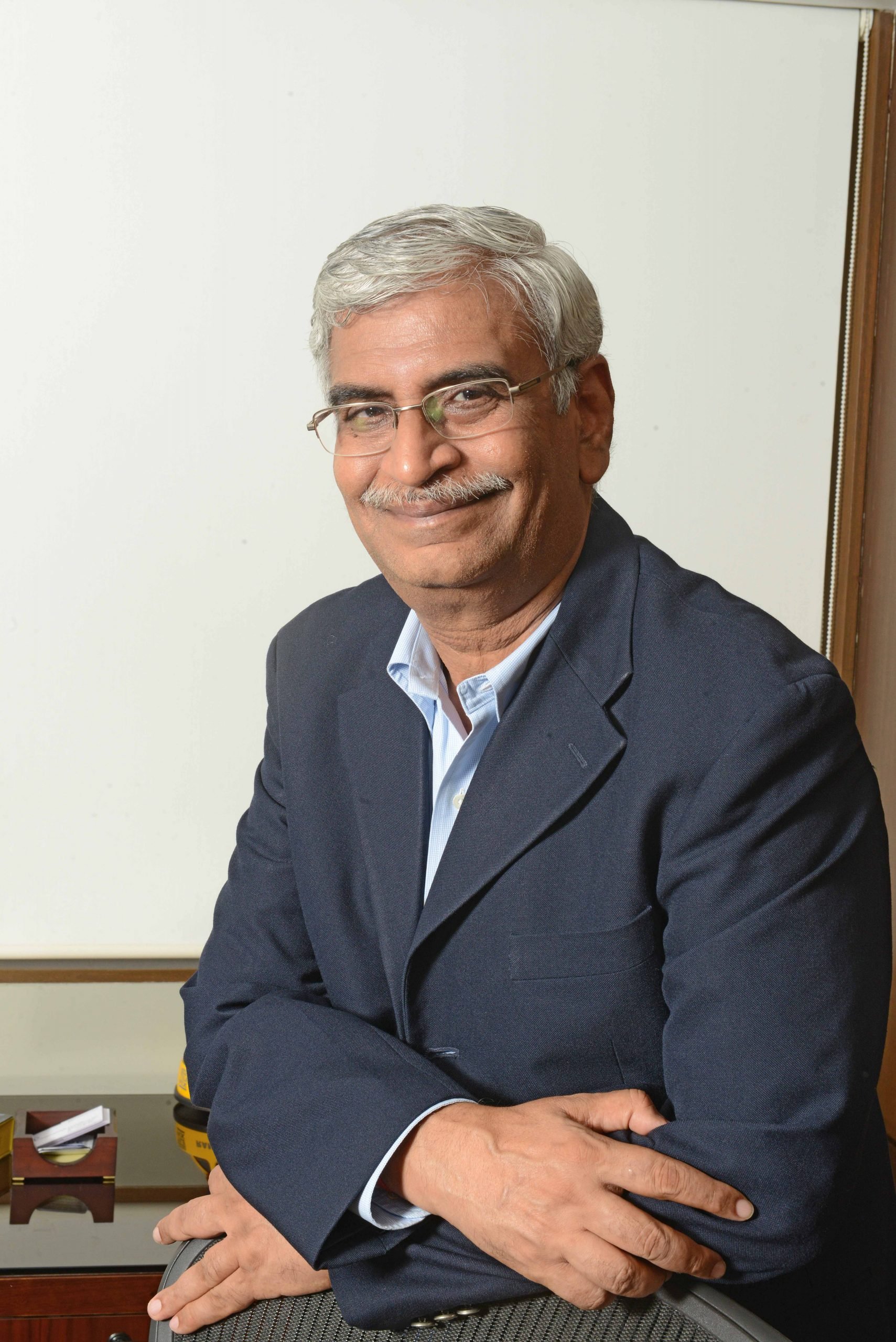
It also assists customers to find solutions for problems they face on particular projects. The R&D centre is responsible for the development of numerous cement products that lead the market in India.
“Our key success is implementing different types of cement for specific applications, and along with that is educating our end users about using the specific types of cement for particular applications,” AVD explains.
“We have a strong technical team to educate customers on the proper use of construction materials and construction methods.
“While our team interacts closely with our customers, they identify their specific needs and inform the operations team about the product attributes needed. Operations, with the help of our R&D division, makes the required changes and rejigs the quality attributes in the product. In that way, the various types of cement are developed so that Ramco always offers the right product for the right application.”
The Ramco Cements – A Timeline
1961 – PAC Ramasamy Raja establishes Madras Cements
1962 – PAC Ramasamy Raja dies. Ramasubrahmaneya Rajha is appointed Managing Director
1962 – Madras Cements’ first plant begins operations at Ramasamy Raja Nagar
1982 – AV Dharmakrishnan joins Madras Cements
1987 – The Jayanthipuram plant in Andhra Pradesh is set up
1993 – The Muppandal Wind Farm is built
1995 – The Poolavadi wind farm is built near Coimbatore
1997 – The Alathiyur facility is established in Tamil Nadu
1999 – Ramco commissions the ready-mix concrete plant in Medavakkam
2001 – The Alathiyur plant is expanded with another line
2002 – A dry mortar plant is established at Sriperumbudur, Tamil Nadu
2005 – The Uthumalai wind farm is built
2009 – The Chenglepet and Salem grinding units and the Ariyalur facility begin operations
2010 – Kolaghat Grinding Unit commences production
2012 – Line two of the Ariyalur plant is commissioned
2015 – Vizag Grinding Unit commences production
2017 – PR Venketrama Raja appointed Chair and Managing Director
2020 – Odisha Grinding Unit commences production
However, the RRDC also investigates allied factors in cement production. Global fuel price rises have had a significant impact on the cost of manufacturing, so Ramco is exploring opportunities and alternatives to mitigate against these rises.
“With the present trend of global fuel price rises, our R&D is focusing on the optimisation of raw mix for reducing the fuel consumption in kilns,” AVD shares. “R&D is also focusing more on the utilisation of waste products and marginal grade limestone as a sustainable measure for conserving natural resources.”
Cement costs
Cement production is cost prohibitive if not closely monitored. The need for very high production volumes while minimising the costs associated with its production necessitates continual improvement in the company’s processes, so AVD has always considered the introduction of new technologies as a primary driver for both higher efficiency and a lower cost base.
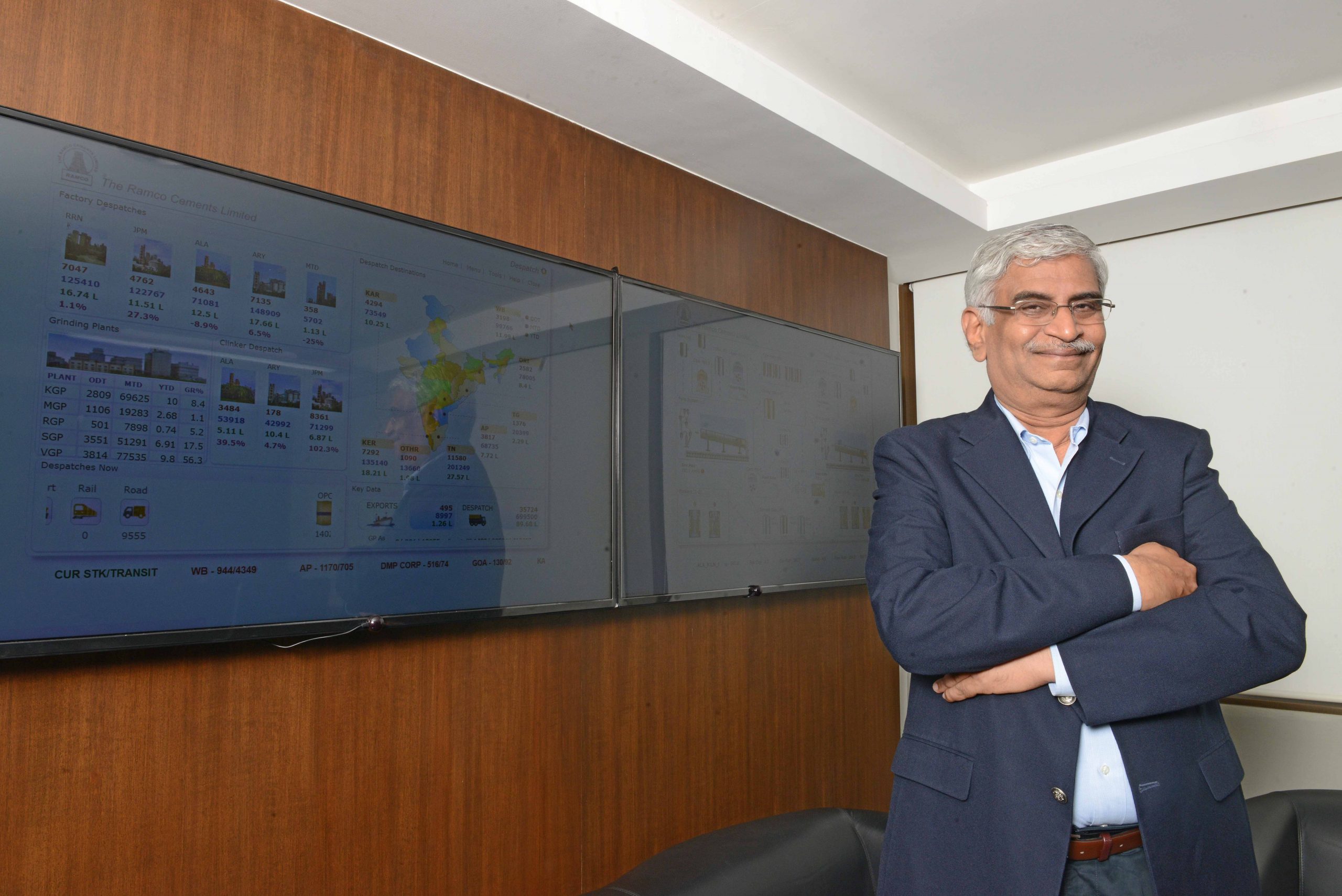
The result of his persistence in exploring new technologies is that Ramco is a pre-eminent cement producer in India and even hosts visitors from its supply company partners wanting to see new technology in action.
It’s a role that AVD is proud of. “In my key area of cement, there are basically two main costs. One is power and fuel, and the other is logistics. If you are able to control these two costs then you will be a leader in this industry, and your profitability will be excellent. You’ll be number one,” he says.
“Our focus at all times is investing in the latest technologies to reduce power and fuel costs. We also have an excellent company-wide information system – I can say it’s the only one of its kind in the world.”
Ramco’s ongoing expansion of its facilities dictates that it must locate new plants in strategically significant zones meeting several criteria, all of which make the choices more difficult. Each plant requires a ready supply of materials, of course, as well as local communities who can provide a labour force, but there are other infrastructure factors that play an essential role in making a site viable as a cement manufacturing location.
“Our biggest challenge is definitely the selection of good factory sites because, being a mineral-based industry, whatever land we select must have high-quality minerals for the manufacture of cement,” AVD points out.
“Our philosophy has always been that every factory should have all the facilities, like appropriate land, the raw materials should be located near the factory, and preferably on the national highway or on a state highway. Each factory should also be near a port, and they should have a railway siding. Without all of these conditions, we normally don’t build a factory. No other cement company in India can claim that they have all those facilities in all their factories.”
Our focus at all times is investing in the latest technologies to reduce power and field costs.
Another major cost base is logistics in storage, transport and handling. Its bulk and heavy weight make cement a difficult product to deal with, hence AVD’s predilection for rail sidings and proximity to major roads. “The only way you can improve this area is to reduce your logistics costs,” he says.
“This plays a very important role in the cement industry. In the past 15 years or more we’ve concentrated on developing various models to reduce our logistics costs, and this is a major part of our success.”
The it factor
AVD has always promoted the use of IT solutions to drive new efficiencies. Not only do new digital technologies improve internal performance, but they also reduce its reliance on old, often manual systems and deliver real-time data for more informed decision-making.
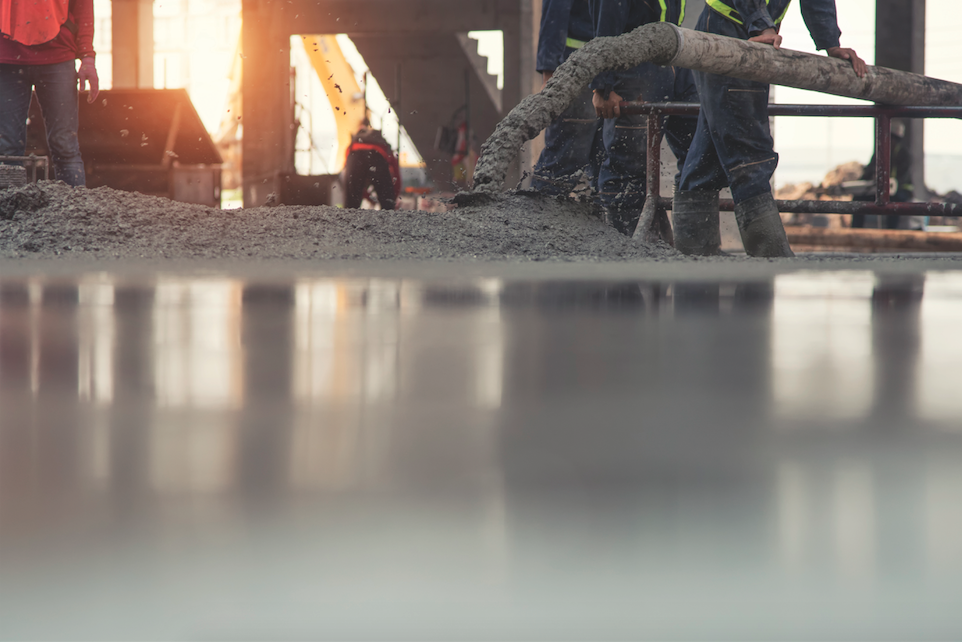
“IT innovation is key to our growth,” AVD affirms, pointing to the company’s computerised accounting systems as an example. Ramco’s salespeople use portable devices for immediate access to dealer and stock information, using an information system developed with Ramco Systems, the sibling software company of The Ramco Cements.
Inventory, transport, damages and much more information is available online for executive decisions based on more accurate planning and production schedules.
Pandemic pressure
The emergence of the COVID-19 pandemic early last year added extra pressure on Ramco in its production and transport operations. Its first priority was to protect its staff from the virus and ensure that suppliers and customers were also protected in their contact with the company.
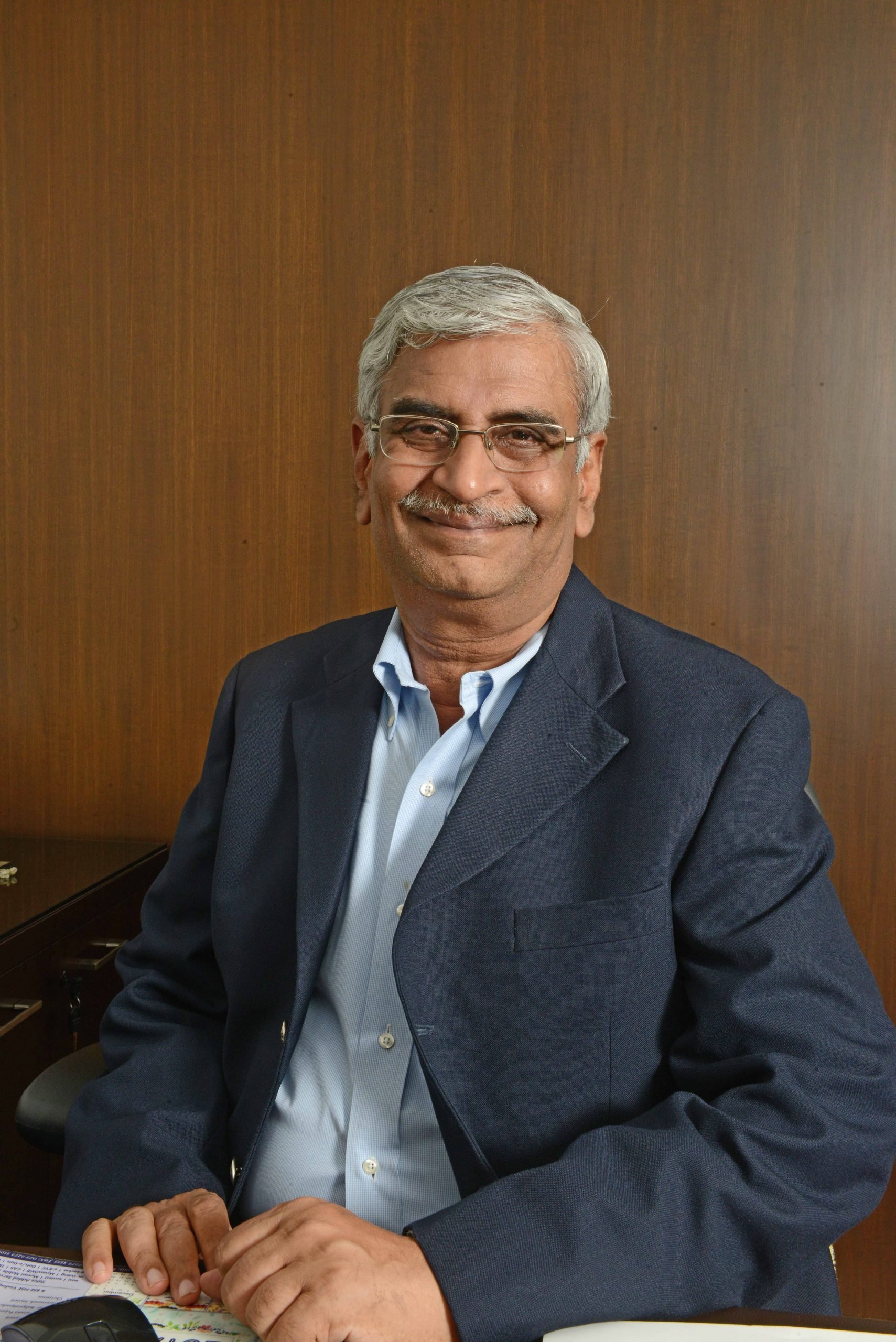
It was a major setback initially, but the company initiated a series of precautions to cover all contingencies. Its efforts were rewarded. “To ensure the highest degree of safety and health for our employees and associates in all our factories, we put measures in place at the beginning of March until the lockdown was announced,” AVD reveals.
The company’s approximately 6,000 migrant labourers and the workers of its forwarding and clearance agencies, even if they weren’t on contracts with Ramco, were given food, shelter and medical attention to ensure they were as safe as possible.
Every worker entering the factory was checked and certified that they were free from virus symptoms, every truck entering Ramco premises was disinfected and the drivers were checked for symptom sand provided with certificates. In addition, all the company’s workers were provided with masks and soap to protect them.
Ramco’s efforts reached out to nearby villages, where doctors and paramedics provided medical attention and water tankers sprayed medicine in the villages to disinfect them and to ensure the safety of villagers. “The safety of the villagers surrounding our plants has always been of utmost importance to us,” AVD confirms.
My greatest strength lies with the well-knitted team I’ve had for many years.
“They have been provided medical attention by our doctors and paramedics.” State governments and district administrations provided welcome support for the company to continue to operate at reduced levels.
Using precautionary measures, it still managed to manufacture and ship about 9,000 tonnes of cement to the Maldives last year. Despite the pandemic and the resultant downturn in economic activity, Ramco is pursuing a vigorous expansion program.
“We have expanded our cement grinding capacity in the state of West Bengal from one million tonnes to two million tonnes,” AVD says.
“We have put up a cement grinding unit in the state of Odisha with a capacity of one million tonnes, and we have also expanded our grinding unit in Visakhapatnam in the state of Andhra Pradesh from one million tonnes to two million tonnes. We’ve increased the clinker capacity in our Jayanthipuram plant in the Krishna district of Andhra Pradesh from 3.2 million tonnes to 4.7 million tonnes, and we’re also setting up a two-million-tonne clinker grinding unit in the Kurnool district of Andhra Pradesh.
Our key message here is always value all your stakeholders, especially your suppliers.
“In the future we will be taking steps into new markets, using our knowledge from our existing plants to calculate how to enter new markets at the cheapest possible cost. Also, we are the first company to go for a vertical roller for cement grinding in South-East Asia.”
Environment awards
With the potential for cement and concrete to be a major environmental problem if not manufactured, handled and used appropriately, Ramco has long pioneered technology developments to help steer the industry to a cleaner future. Its environmental R&D efforts have been rewarded with numerous awards for more than a decade.
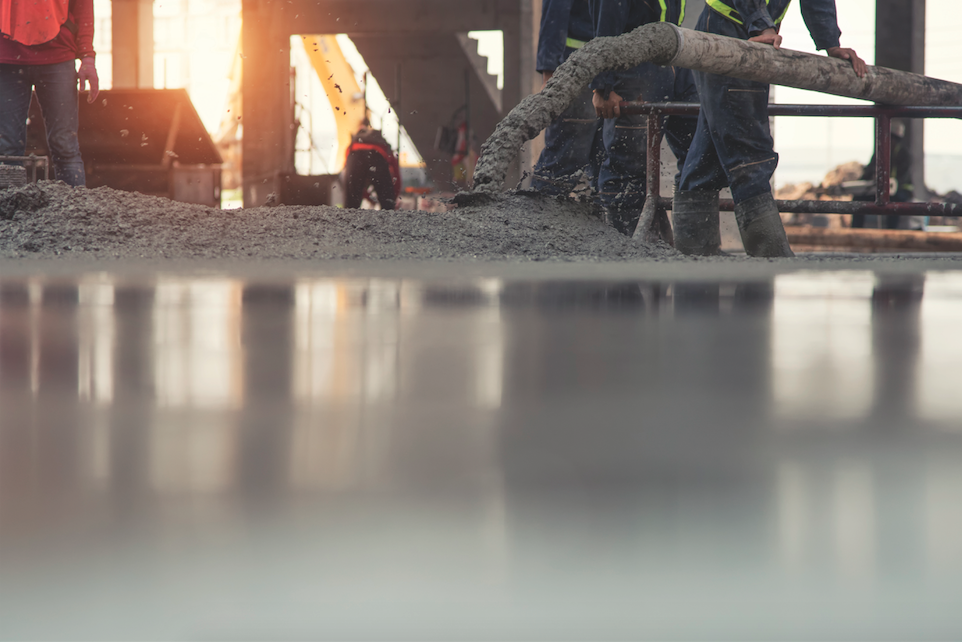
It was the only cement manufacturing company to win the Four Leaves Award, given by the Centre for Science and Environment, for ensuring dust-free and clean factory premises at its facilities.
Its Jayanthipuram unit was also the winner of the Cleaner Production Measures Award from the Andhra Pradesh Pollution Control Board and Government Ministry of Environment, Forest and Climate Change.
The company’s Alathiyur facility won the CII Environmental Best Practices Award in 2012, and the Ramasamy Raja Nagar and Alathiyur plants were winners of the Best Improvement in Electrical Energy Performance 2014-15, which was presented by the National Council for Cement and Building Materials.
Counting on partners
Ramco’s expansion plans and growing market volume mean that the company’s supply chains are paramount for efficient production and logistics. The pandemic only accentuated its reliance on the partnerships it has developed over the past six decades, a central plank in the company’s success.
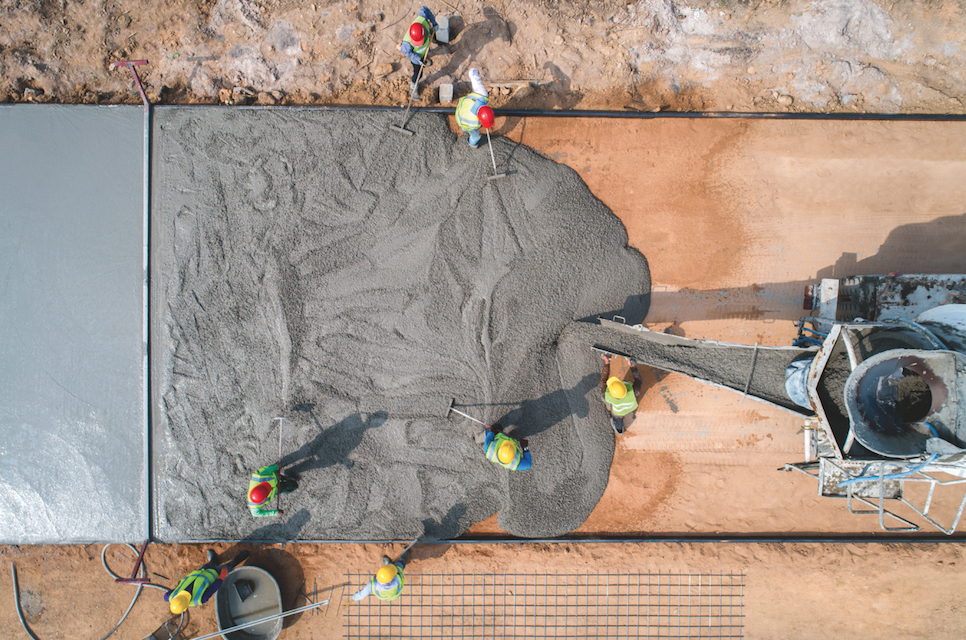
“As far as Ramco is concerned, our suppliers are long-term partners and not just machinery suppliers based on a specific quotation,” AVD asserts.
“We work with the technical teams of machinery suppliers to adopt the latest technology available in the market today. Same-day delivery is expected in the industry, so as cement producers we must be highly organised to avoid inefficiencies in this area.
“The company has forged strong ties with its suppliers, and respect is the key to maintaining these relationships. The philosophy of our former Chair, PR Ramasubrahmaneya Rajha, was to not take your suppliers for granted and not to milk them, and to instead treat them as equal partners. This has been the approach I have adhered to with this company.
“When we have good relationships with contractors and suppliers, we’ll deal with them forever. That is one of our basic values, ensuring all our stakeholders have been taken care of, including our delivery network. Cement is a low-value, high-volume industry and in this context, distribution becomes extremely important.”
Inclusive culture
From the beginning, Ramco has invested in its workers with training and skills development, but also by creating a corporate culture that builds trust and confidence in staff wherever they are employed.
With so many locations and facilities, maintaining a common culture among them all is a priority to ensure that each facility contributes consistently to the company’s overall performance. That reaches back to the company’s foundation in 1961, AVD says.
“We follow our founder’s strong belief in ethical values, leadership qualities and motivation to form a committed team,” he insists. “He laid a strong foundation for steady growth of the company, and the company’s keen interest in the welfare of our employees and shareholders is unique and unparalleled. A commitment to work to achieve continuous growth in the company is the mantra of our employees, right from the inception of Ramco.”
AVD prefers to divert attention away from the contribution of his own managerial skills, developed over three decades at Ramco, to the development of that company ethos. He points to his leadership team as the real strength of the organisation and its ongoing success.
“My greatest strength lies with the well-knitted team I’ve had for many years,” he says. “We understand each other’s abilities and we complement each other. A key measure of our success is definitely the level of professionalism within the company. Our core team has been with me for the past 25 years or more. They understand me and I understand them. As we’ve been together for so long, I understand the strengths and weaknesses of individuals, and they understand my own strengths and weaknesses!”
Setting challenges
With three decades at the company, AVD has seen the vicissitudes of the cement and construction industries in India come and go. Those industries are reliant on gaining regular finance, a stable economy and solid employment prospects over extended periods to see major projects come to fruition.
Those years have taught him resilience, determination to push through barriers and patience for eventual rewards to those who wait. It was an early project in his career at Ramco that springs to mind for its complexity and difficulty in getting finance to ensure the project got off the ground. It was an object lesson for him.
“In 1986, when I’d been at Ramco Cements for just four years, the management team had given me the responsibility of CFO, which was a very challenging position at that time because the company was engaging in an expansion project in the state of Andhra Pradesh,” he admits.
“In the 1980s, institutional finance was restricted to just two or three institutions. “Meeting institutions to get finance for the project was very difficult. The expansion of the Jayanthipuram project and also the initial challenges in implementation gave me a great insight into understanding not only finance, but marketing as well. Over a period of time, I gained a lot of knowledge in the processes and technology of cement too.”
AVD also remembers advice given to him by PR Ramasubrahmaneya Rajha. “Dedication to your work is the best advice I received from our former Chair,” he says. “Our key message here is always value all your stakeholders, especially your suppliers. If you accept them as your equal partner and provide value to them, they’ll help you. “That is my experience in this company.”
Proudly supported by:
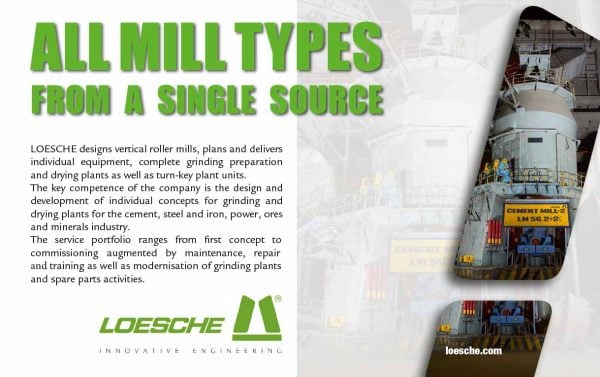
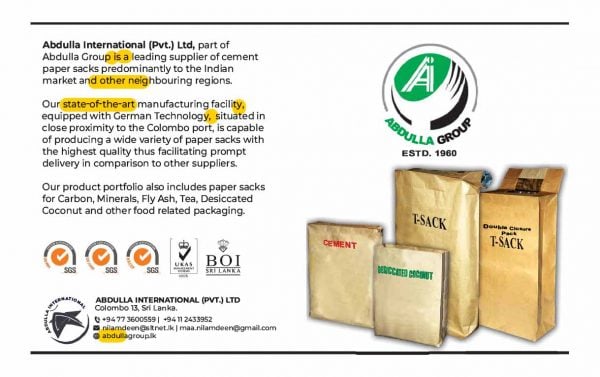
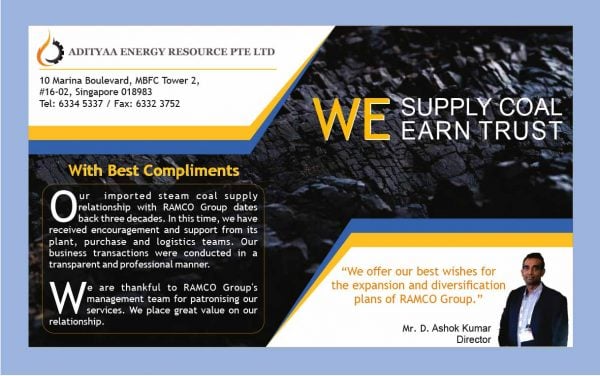
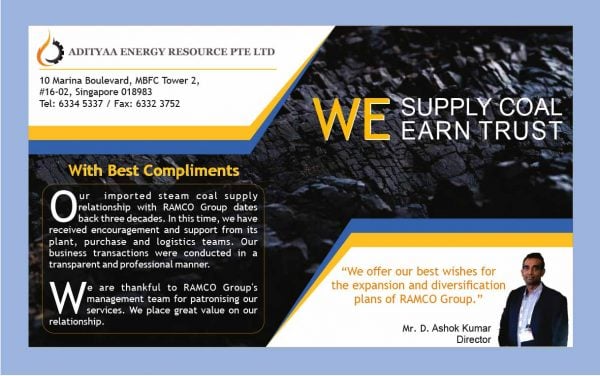
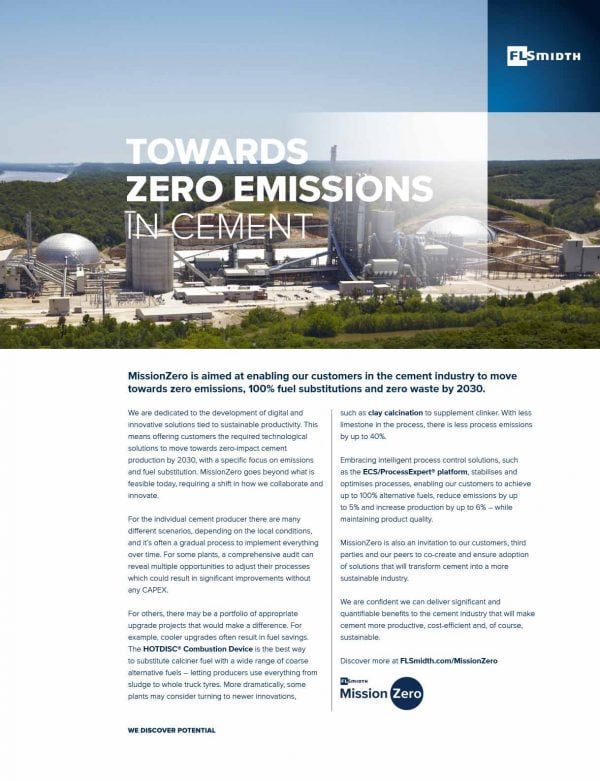
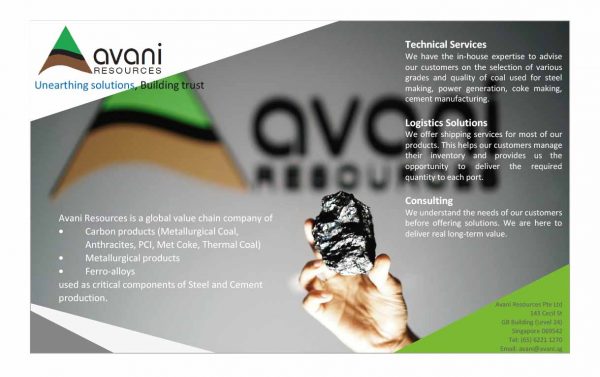

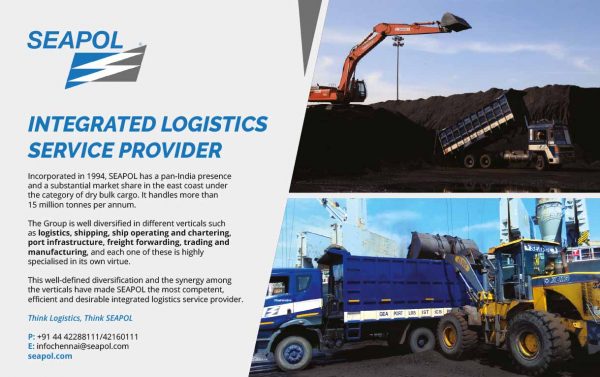
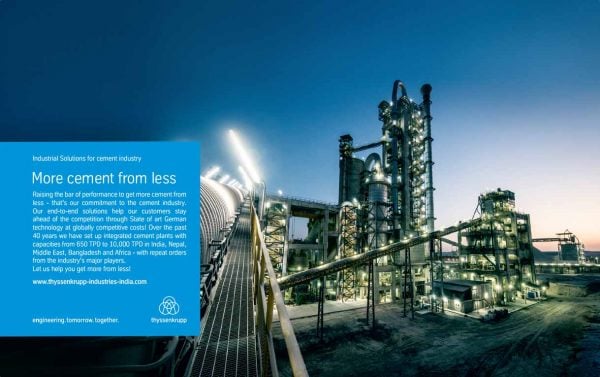