Say the word semiconductor and most people’s eyes start to glaze over. But with our ever-increasing reliance on these fingertip-sized specks of technology, Tan Yew Kong predicts that’s all about to change.
“This is an exciting time for the world to appreciate this industry better,” the Senior Vice President and General Manager of GlobalFoundries Singapore tells The CEO Magazine.
In today’s highly digitalised world, everything we do – or aspire to do – is enabled by these small, yet highly complex chips that power smartphones, computers, appliances, medical equipment and even electric vehicles. “The potential of this industry to develop innovative solutions to make life better is enormous,” he enthuses.
Case in point: GlobalFoundries (GF) chips powered micro controllers, which were used to maintain the low temperatures required in the transportation process for COVID-19 vaccines during the pandemic.
For Yew Kong, this example illustrates exactly how semiconductor manufacturers like GF can do their part to help the world. “Today, we’ve moved beyond just manufacturing chips that go in devices like smartphones and other electronic gadgets,” he says. “It’s also about how we partner with and enable our customers to innovate and impact humanity. And that’s one of the missions of GF.”
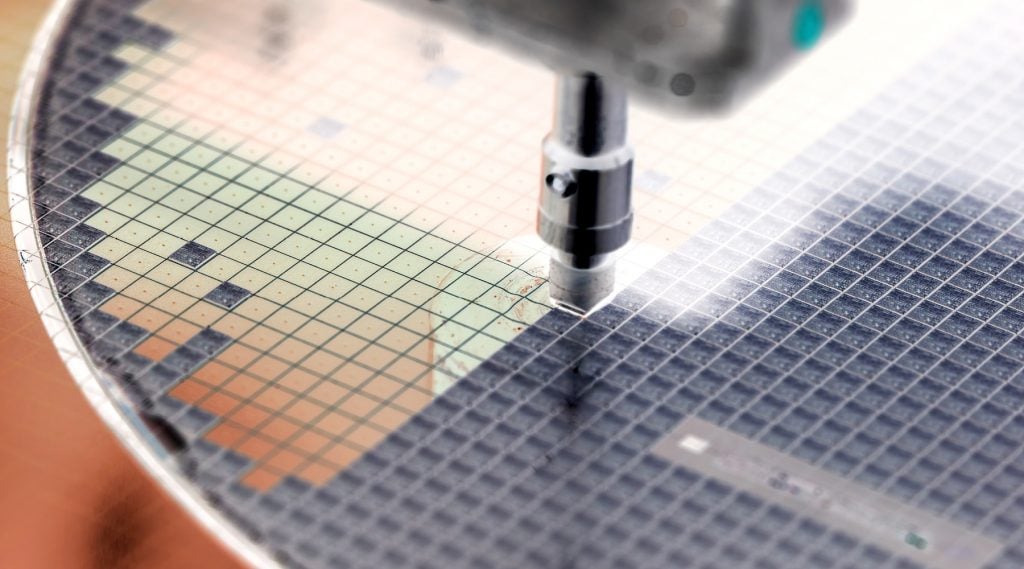
Time flies
One of the world’s leading names in semiconductor manufacturing, GF was formed by a joint venture between Mubadala Investment Group – the Abu Dhabi government’s sovereign wealth fund – and Advanced Micro Devices (AMD) in 2009.
Since then, the company has built up a global footprint, with manufacturing sites across three continents including Singapore, the United States and Germany. It was successfully listed on the NASDAQ Stock Exchange in 2021.
It is in Singapore where Yew Kong has spent 27 years of his career. He started his semiconductor journey in 1995 when he joined Chartered Semiconductor, at a time when the semiconductor industry was just beginning to gain traction in the country. Chartered Semiconductor was eventually acquired by GF in 2010.
Yew Kong graduated from the University of Wisconsin-Madison with a Master of Science in Mechanical Engineering before joining GF in 1995, where he progressed from manufacturing to lithography engineering. Thereafter, he took on a role as a department head, becoming the General Manager of the 200mm Fab in Singapore in 2013.
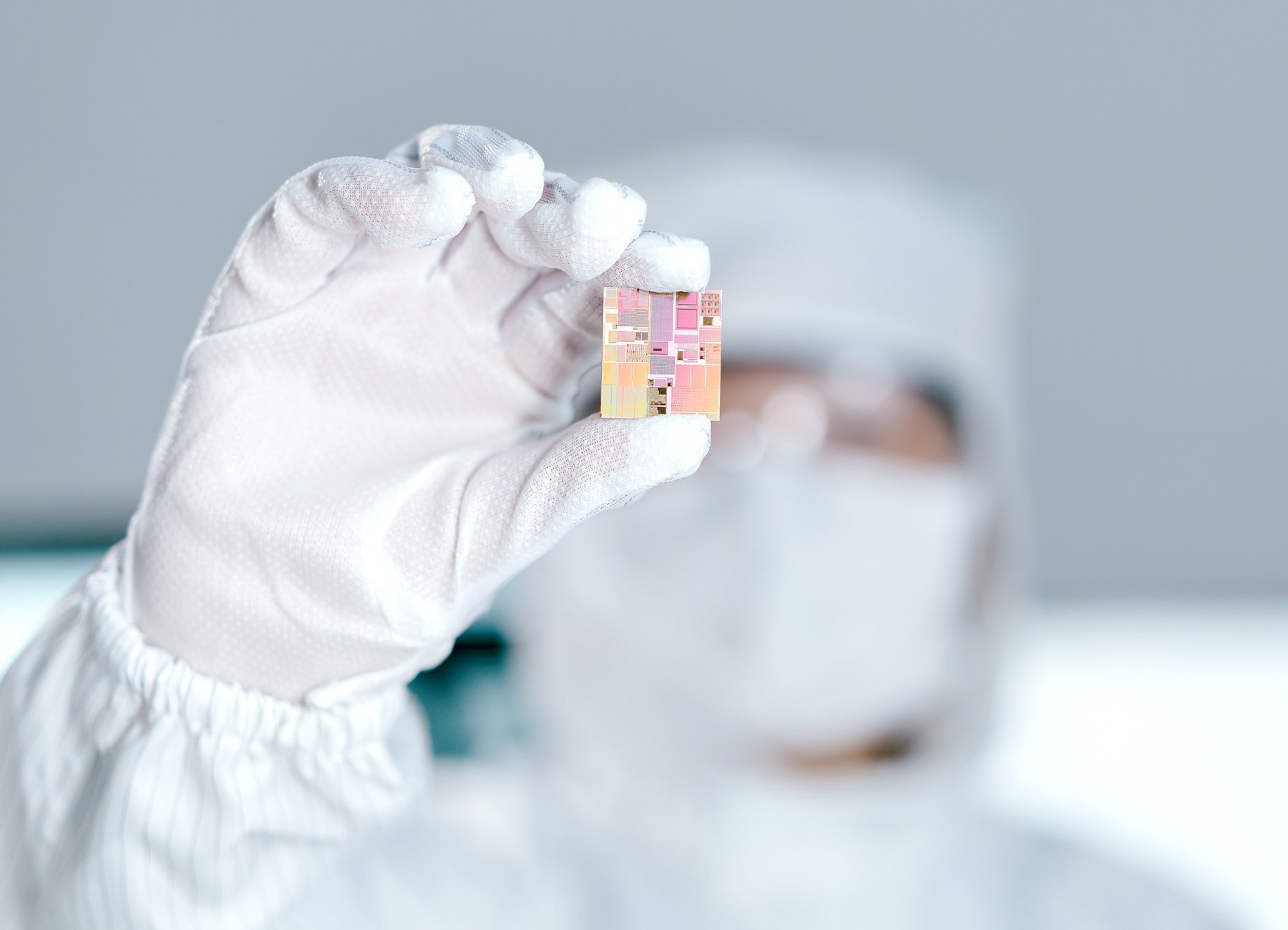
If you tear down any 5G-enabled phone, if you look inside any car, you’ll find chips that have been made by GlobalFoundries.
In 2019, Yew Kong assumed the role of General Manager of Fab 7 (300mm), where he managed a team of over 1,600 staff to manufacture feature-rich radio frequency, embedded memory and analog power solutions for using semiconductor technology between 130–40 nanometer nodes. The chips shipped from this foundry are destined for smartphones, automotive systems and internet-of-things applications, among other products.
Yew Kong took on the responsibility of the entire Singapore site as Senior Vice President and General Manager of GF Singapore in 2022. “It has been 27 years, but believe me, time flies because no two days are the same,” he says.
“Every decade or so in the past, we have seen a single mega trend driving the demand for semiconductors, such as adoption of personal computers, internet connectivity driving the demand for enterprise servers, and adoption of mobile devices.
“Today, we are experiencing several mega trends concurrently, driving the demand for semiconductors such as Internet of Things, 5G adoption, artificial intelligence and the automotive sector.”
Essential service
In a sector experiencing high pace of change, the semiconductor industry has remained resilient over the years. This was especially apparent during the COVID-19 pandemic. Considered an essential workforce sector by the Singapore government, GF’s local site remained open throughout the pandemic. The high level of automation in Fab 7 meant that GF Singapore could maintain production of its semiconductor chips with fewer team members on site due to social distancing measures.
“The key leadership team met almost weekly to discuss how the pandemic was evolving, what the latest was from the government and how we could run our business while keeping our team safe and healthy,” he says.
If there’s one example of agility in the face of the health crisis that he’s particularly proud of, it’s the speed at which he and his team were able to react to Malaysia announcing its imminent lockdown in March 2020. “A big portion of our workforce does the daily commute from Malaysia,” he explains.
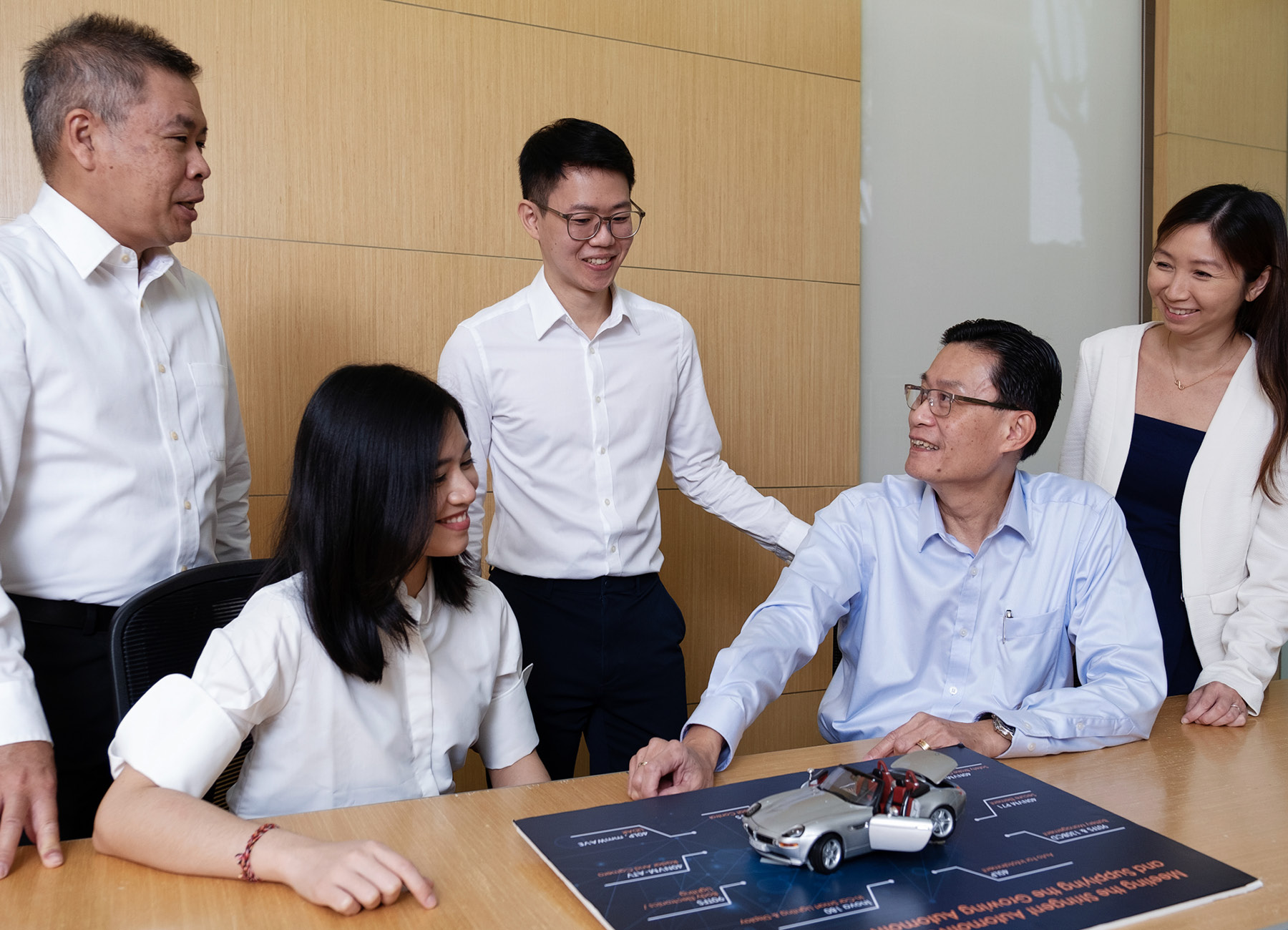
We could produce what our customers needed on more than one continent.
Fortunately, having grasped the gravity of the situation, Yew Kong had already challenged his team to build the capabilities to control the factory operations remotely. “So, by the time Malaysia announced it was going to shut down the border the next day, we had been pushing for the technology to be ready,” he says.
The day of the announcement, a team quickly purchased, configured and dispatched 80 iPads to employees returning to Malaysia before the border closed, allowing operations to continue uninterrupted.
“Despite all the challenges we faced during the pandemic, I am proud that the team still managed to meet our production targets without missing a beat. Thanks to the Singapore team for being such a committed, supportive and motivated workforce,” adds Yew Kong.
On the business front, it was an entirely different story. “Demand really picked up,” he explains, acknowledging the sudden increase in demand for semiconductors due to accelerated digital adoptions triggered by the pandemic. “Forced to stay at home and work and study from home, people needed laptops, the internet, they needed connectivity,” he adds.
With all its capacity taken up by connectivity customers, Yew Kong says that when the automakers started to place orders again, they could not supply enough chips to match their customers’ requirements. This supply shortage situation really brought home just how critically important these tiny chips are.
For GF in particular, its global manufacturing footprint really came to the fore. “It allowed us the flexibility to produce what our customers needed on more than one continent,” he says, adding that, for instance, Fab 7 in Singapore has overlaps on technology platforms that are dual qualified with its Dresden facility, so that GF can shift production from one facility to another.

Fab 7
In GlobalFoundries FoundryFiles blog, Yew Kong discusses what makes Fab 7 unique among the company’s global fabs.
“We work with more technologies than any other GF fab, which supports GF’s ability to offer a very wide range of truly differentiated solutions,” he says.
It’s a situation that brings its own particular set of challenges, however. “In a given year, Fab 7 will have more than 1,000 different chip designs from around 200 customers in production. This has resulted in high production complexity and requires a high level of skill, talent and dedication on the part of our team to deliver quality wafers on time and consistently.”
Increased capacity
So much has the business evolved since early 2020 that last year ground was broken on a new US$4 billion fab in Singapore, in partnership with the Economic Development Board and other customer investments. With the first tool installed one year after ground-breaking of the new Singapore Fab Expansion in June 2022, the development marks an important step for the business as it looks to increase its production capacity to meet global demand for its semiconductors.
Since then, GF has moved in more than 250 tools and remains on track for commencing production in early 2023. “Our current factories aren’t sufficient to support the industry, so increasing our manufacturing capacities is a must,” Yew Kong explains.
According to industry and analyst estimates, the global semiconductor industry is expected to grow into a trillion-dollar market in the next eight-to-10 years.
In line with its global expansion plans, GF also announced a partnership with ST Micro to open a new facility in Crolles, France. At the same time, the United States government also passed the US$52 billion CHIPS and Science Act, which has levelled the playing field for semiconductor manufacturing in the United States.
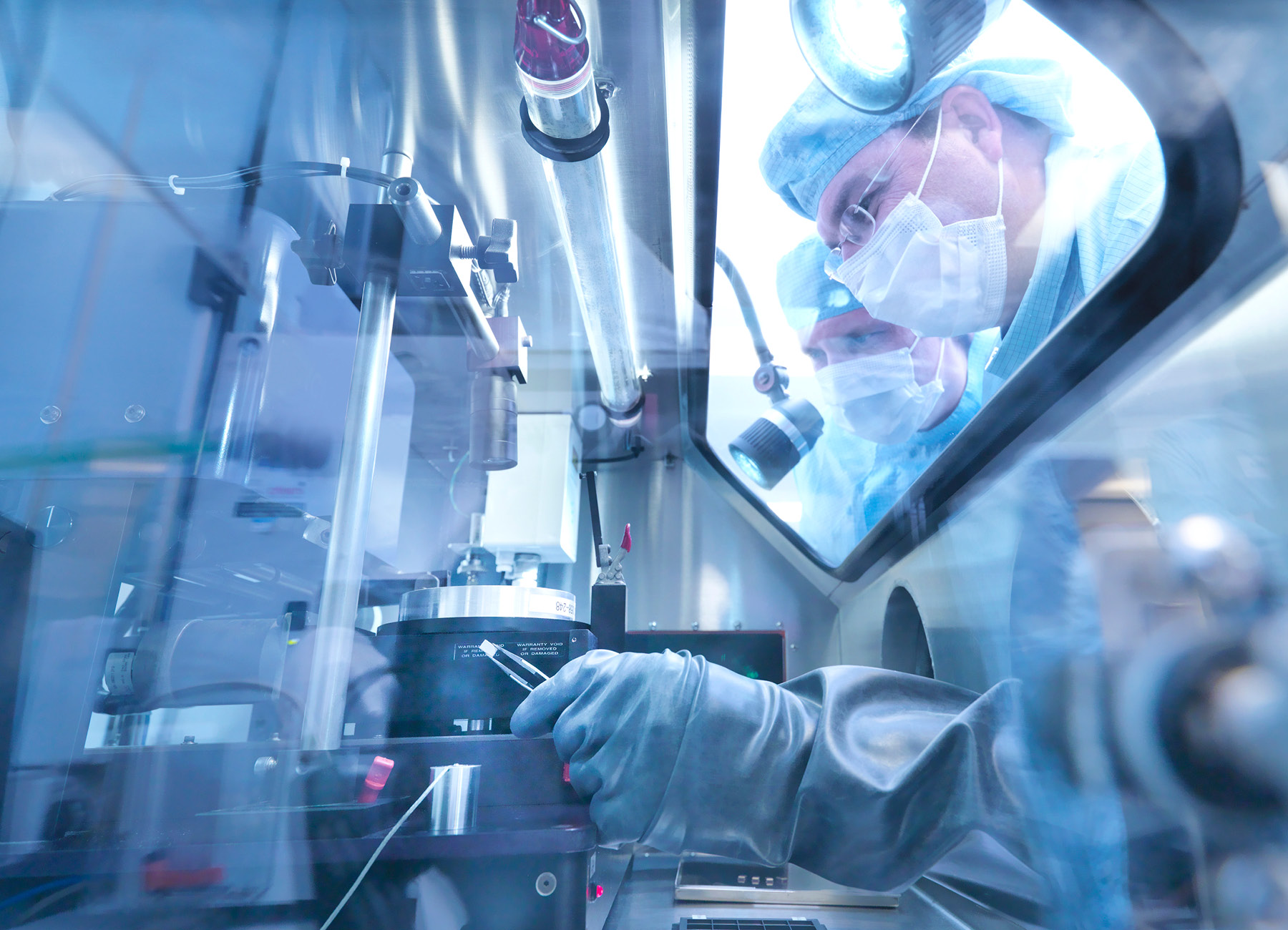
As long as there is the business to support it, we will continue to build more factories.
And, while the GF Executive Board, led by CEO Dr Thomas Caufield, is eyeing off expansions in the US and Germany, there’s also plenty of scope for continued growth in Singapore. “As long as there is the business to support it, we will continue to build more factories,” he asserts.
Yew Kong is also aware that beyond the best interests of the company and its clients, there’s also the contribution of the industry to the country. “The manufacturing sector accounts for 20 per cent of Singapore’s GDP,” he says. “And because of this heightened interest in semiconductors, we have a lot of momentum and support on this front.”
While GF continues to expand its global manufacturing capacity, the company is committed to doing so in a sustainable manner through its Journey to Zero carbon goal, to reduce total greenhouse gas emissions by 25 per cent by 2030.
Another bonus to emerge from the semiconductor boom is a modern and inspiring career path to promote to students in Singapore’s universities and polytechnics. “To capitalise on what has changed in the last two years, we are working closely with bodies such as the Economic Development Board, the Singapore Semiconductor Industry Association, and partnering with institutes of higher learning in Singapore to attract talent to this very exciting industry.”
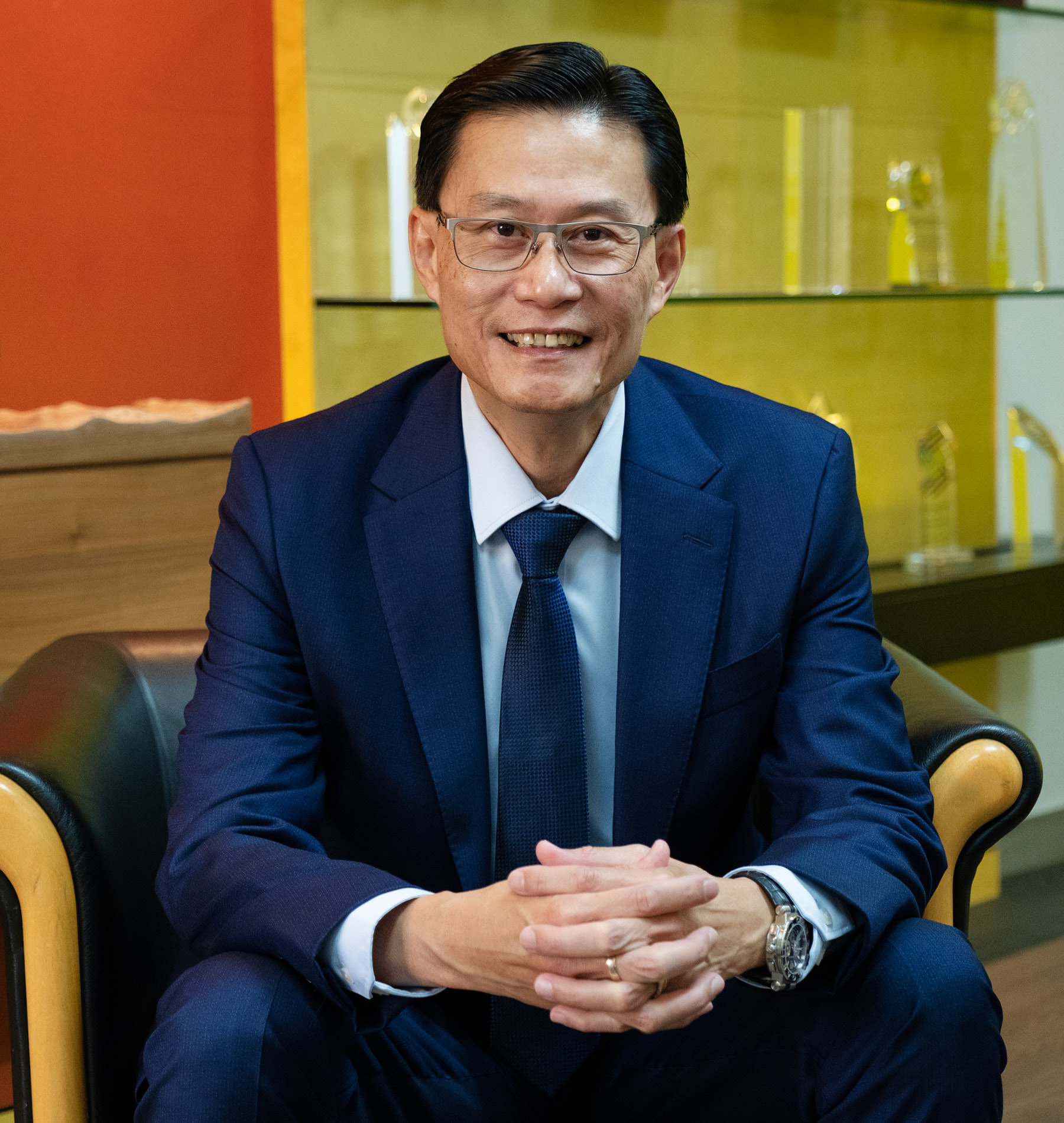
Leadership Rules
Yew Kong’s three key leadership components:
1. Appreciation: “You need to appreciate people for who they are as a person as well as for the background they come from. At GF, we truly believe in embracing our teams under our global umbrella of diversity, equity and inclusion.”
2. Foresight: “You need to be able to look ahead and prepare for changes and be ready for change.”
3. Flexibility: “You need to evolve as the world and technology do. You can’t have a one-size-fits-all approach. You need to be flexible to change as circumstances do.”
There’s another challenge GF faces: “We make the chips that power the products, but the end consumers may not know who we are,” he says.
As our understanding and awareness of the importance of semiconductors increases, it’s also time for the spotlight to be placed on the people making them.
“Now’s the moment for us to actively shout about what we are making. If you tear down any 5G-enabled phone, if you look inside any car, you’ll find chips that have been made by GlobalFoundries. Indeed, GF has been living up to its vision of ‘changing the industry that is changing the world’.”
Proudly supported by:
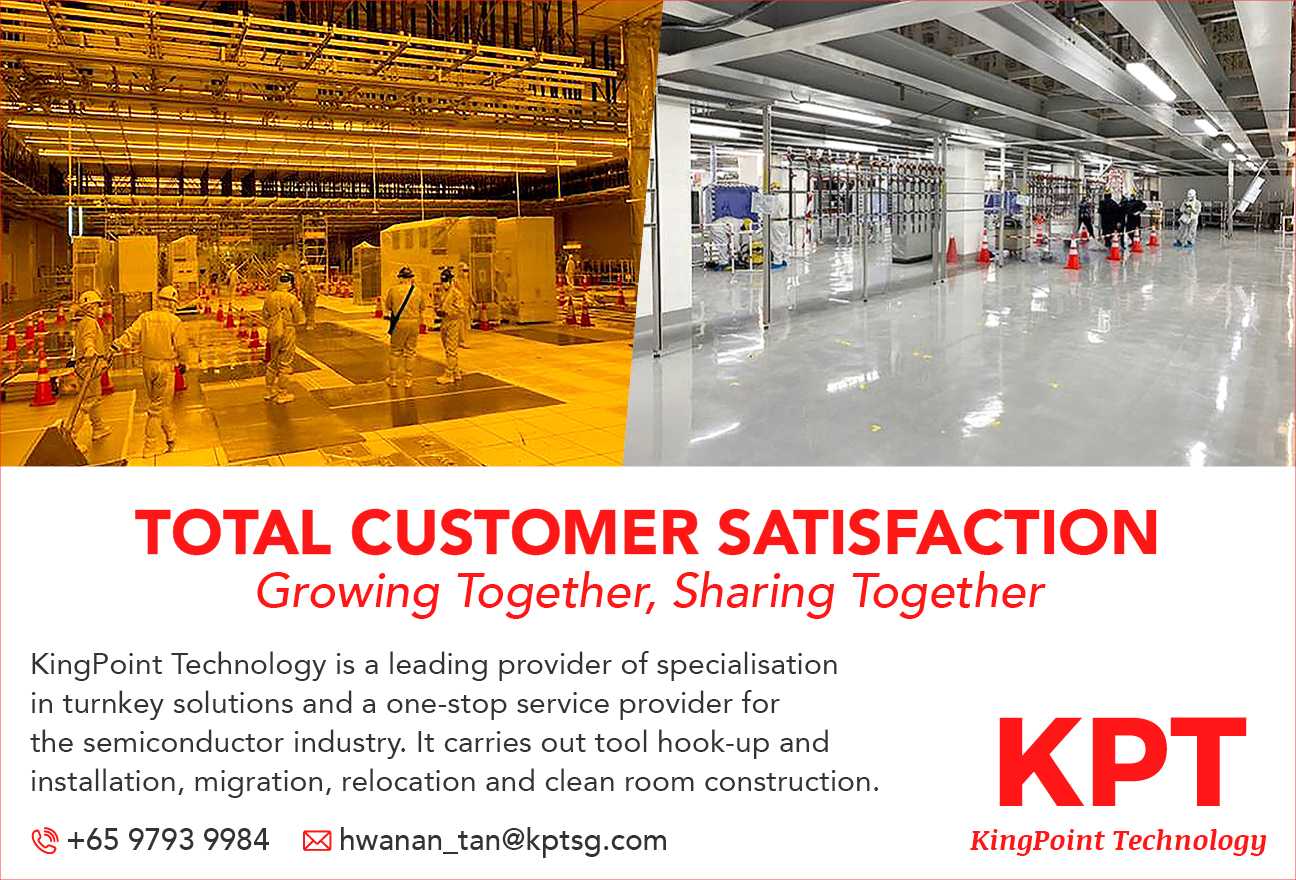