With one of its factories based in China, Perlen Packaging was among the first European companies to be hit by lockdown restrictions as the novel coronavirus began to spread with greater speed in early 2020.

In February of that year, before the World Health Organization had declared COVID-19 a pandemic, the Chinese government ordered Perlen Packaging’s facility in Wujiang to close amid stringent nationwide restrictions aimed at curbing the virus. At the time, it felt like an enormous blow to a company focusing on emerging markets as part of its global growth strategy.
The Switzerland-based company had just enjoyed a record year of sales and was on its way to achieving more. Now, one of its key facilities in a major growth market was out of action. But Perlen Packaging was in the right business for this crisis.
The company specialises in making packaging for the pharmaceutical industry and as such, its factory was among the first that the Chinese government allowed to resume operations because it was considered so vital to the country’s response to the virus.
“We were one of the first plants in China that were allowed to reopen, and we were able to do that because a factory making packaging materials for the pharmaceutical industry is considered a system-relevant facility,” recalls CEO Wolfgang Grimm, who has spent more than 20 years working in the packaging industry and joined the group in 1998 as Managing Director of Perlen Converting.
We are now collecting a lot of data from our processes, and the idea behind it is that we have a good, constant and reliable quality, and we can guarantee that we operate with the same quality worldwide.
“We were able to open back up, but only very slowly because of the measures in China. We were not allowed to use all of our staff because quite a few of our Chinese employees were still in other districts or other regions, so we were only able to start with 50% of our employees, and then slowly we were able to get back to full employment.”
But the real challenge came when the crisis arrived in Europe and drug manufacturers began sharply increasing output. “What we saw then was an extreme order intake, so March and April were the highest months of order intake we’ve ever had – historic levels,” Wolfgang says.
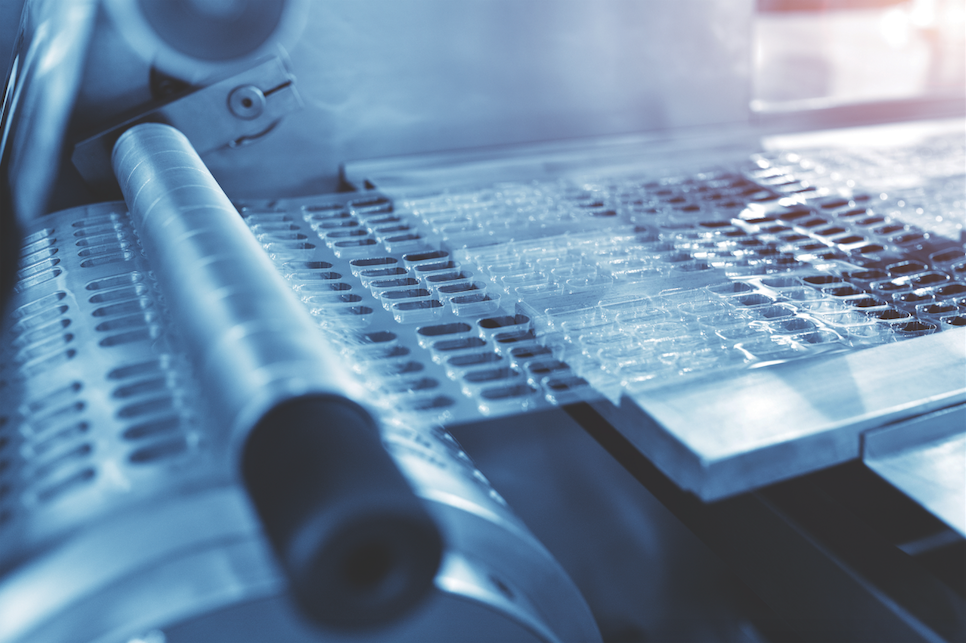
While in theory this was a positive sign for the company, Perlen Packaging had to respond rapidly to avoid being overwhelmed. “It was very difficult to cope with the workload that we had, which was mainly coming from Europe,” he admits.
“Everybody was ordering, including customers that were normally not on our customer list. Everybody tried to get material, so we were really confronted with the challenge that all of a sudden our capacities were more or less overstretched.”
Wolfgang is proud to say that he and his team rose to the occasion. “We took some measures to balance things within the packaging facilities, to balance the workloads so we were then able also to use some of the capacity we have in China, where we were still not working at full capacity. We shifted some business to China in order to keep our lead times globally at a decent level,” he reveals.
You have to monitor the market and be aware of what’s going on while trying to use new things which are coming on the market.” “you have to monitor the market and be aware of what’s going on while trying to use new things which are coming on the market.
The result is that after a tough start, 2020 ended up being another stellar year for sales and at the time of writing, Perlen Packaging was shaping up to the CHF162 million (€150 million) in net sales it made in 2020.
Latin American Growth
Tracing its history back to 1954, Perlen Packaging is one of the only packaging companies focusing specifically on pharmaceuticals. Employing around 420 people, it supplies 40,000 tonnes of packaging materials to 85 countries each year, and has state-ofthe-art facilities in Switzerland, Germany, the US, China and Brazil.
Over the course of six decades, Perlen Packaging has earned itself a reputation within the industry for exceptional standards. “Our processes and facilities are really geared toward pharmaceuticals,” Wolfgang explains.
“Everything is audited. We have a high manufacturing practice level. We have high process standards, and we are known to have high technical standard equipment throughout the factories, so that we can fulfil the requirements of the industry better than possibly other companies can.”
One of the reasons Perlen Packaging opened the Wujiang factory in 2016 was because many of its customers had also set up offices and facilities in the region. Being on the ground there meant that it was not only poised to be part of expected double-digit growth in pharmaceuticals, but it could also be reactive and flexible to the needs of its customers, according to Wolfgang.
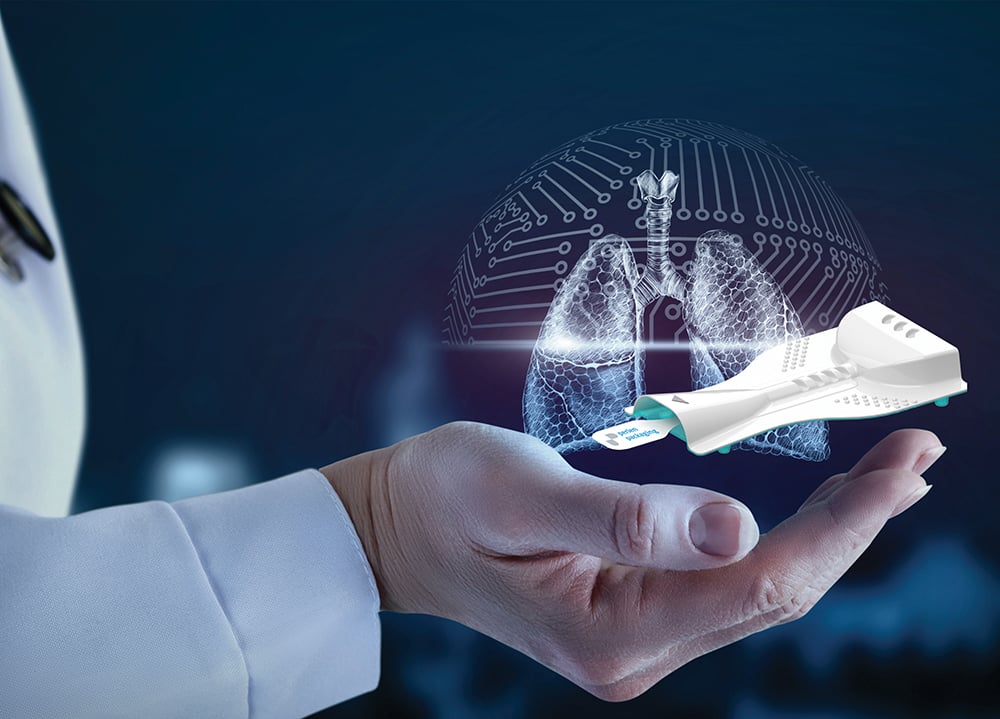
In 2018, the company extended its reach into emerging markets by acquiring a 60% holding in Brazil’s Sekoya Indústria e Comércio, which now trades as Perlen Packaging Anápolis.
The firm’s blister film cutting and logistics operation, which employs 20 people, has helped Perlen Packaging’s Latin American sales reach double-digit growth since the acquisition.
More recently, keen to benefit from the fact that Brazil is the world’s sixth-largest pharmaceuticals market, Perlen Packaging announced it was expanding its operations there by building a new polyvinylidene chloride (PVdC) film coating plant with the capacity to produce 6,500 tonnes of the material per year.
(PVdC is a transparent polymer that is very effective at keeping moisture and gases from passing through.) The new plant is expected to start its operations in early 2022, and Perlen Packaging is supporting its Brazilian business partner to build a separate mono PVC film factory at the Anápolis site too.
We have the spirit of continuous improvement in our team, and we are not afraid of challenging any new segments or any new requirements.
The remaining 40% of the company was bought in late 2020. Perlen Packaging is now the sole owner of Perlen Packaging Ltda, Anápolis, as part of a plan to benefit from the expected 9% growth in Latin America’s pharmaceutical industry by 2024.
“We’ll then have a full production scope down in Brazil in order to furnish or to deliver to the South American markets – mainly Brazil, but also the whole South American area, which is one of the fast-growing areas in the pharmaceutical business,” Wolfgang shares.
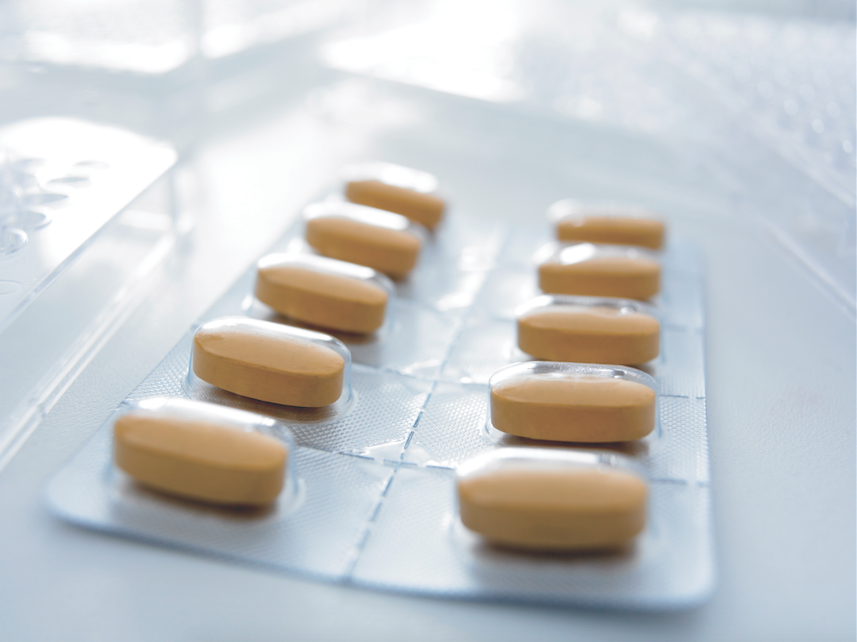
“And with that, we will finalise the global production presence of Perlen Packaging all over the world. So China is one, then we have Europe, we have Switzerland, we also have the US.” Asia now represents roughly 20% of the company’s sales, while the Americas represent another 20. That is expected to grow, he says, but in 2020, “Europe was still the main driver of the business”.
Outdoing the market
Perlen Packaging is one of three divisions under the CPH Group, with its two sister companies working in chemicals and paper. One reason behind its emerging market expansion is the Group’s desire to offset the difficulties facing the paper part of its business. The Group also wants to become less reliant on the Swiss franc, Wolfgang explains.
“To raise the share of sales outside Europe, we’re following the strategy of Asia and South America, and then there is also a certain importance to reduce the currency dependence on the Swiss franc,” he says.
“And that means expanding capacity outside Switzerland. “And then it’s about expanding this business unit in particular – packaging – to a higher extent in relation to the paper business, to balance that better. As you can see, the paper market is a difficult market. It’s consolidating and we in packaging, in the pharmaceutical market, we are in the growth area.”
While Europe still accounts for the majority of sales, emerging markets are expected to help Perlen Packaging grow faster than the market at large. The company has made “an important step” towards hitting yearly revenues of CHF200 million (€184 million) and now it has its sights on reaching six to 7% growth per year.
“Our strategy is also that we grow faster than the market, so we are very much on track with expanding markets outside Europe,” Wolfgang says. Another way he hopes the company will stay ahead of the market is through product innovation.
In 2017, Perlen Packaging unveiled the BLISTair, the world’s first disposable single-use inhaler, which helped the company flex its muscle as a forwardlooking innovator.
The device, which can be used to deliver pain medications and vaccinations or in response to heart attacks and anaphylactic shocks, won numerous awards, including the Best Drug Delivery Device in the CPhI Pharma Awards 2017 and the Swiss Packaging Award 2018.
It was also named winner of the World Packaging Organisation WorldStar Packaging Award 2018. The product design is relatively simple. It is made with two thermo-formed films that enclose the drug that is to be delivered into the lungs.
It therefore has a low manufacturing cost and, according to Wolfgang, means Perlen Packaging has moved beyond just supplying packaging to customers to now enabling it to enter new markets that were previously inaccessible because of the costs involved in packaging inhalable drugs.
It makes many emerging markets more accessible to customers because consumers with less spending power can be reached with the new, low-cost inhaler.
“Now we are trying to go a step further with interested customers to try to make agreements with them on concluding development products, where we then bring our BLISTair into the picture and approach the pharmaceutical industry, so we can prove it is a feasible product for this market segment,” he says.
Last year, the company introduced a new ultrahigh-barrier film, the MultiLayer ultra 280, to the market. The PVdC-based film is used to make blister packs and offers customers more square metres of packaging per kilogram of material, making it more efficient.
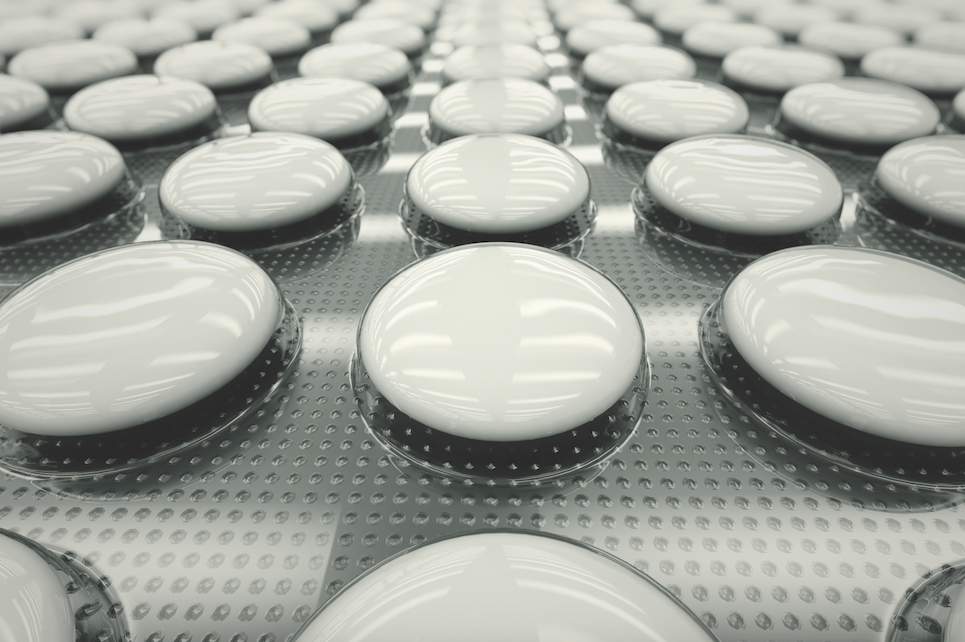
This new product is a perfect example of Perlen Packaging innovating with its customers’ needs in mind: it is optimised for gap heating machines and designed to form at lower temperatures. It also has two identical outer layers surrounding the inner layer, meaning there is no risk of the customer mixing up the inside and the outside when feeding it into their machines.
“We consider ourselves a market leader in high-barrier films, so that is one of the main areas where we are introducing new products,” Wolfgang adds.
Quality across the board
Perlen Packaging is optimising its operations at the production level too, bringing in new automated machine technologies to help set, cut, pack and finish the products “to be of better service” to customers, Wolfgang suggests.
“We are installing that in our facility in Germany, and also new machinery has been put in China and Switzerland.” “Another part of that process is to collect and monitor the data from the production and bring that together with our ERP system, so we can improve the processes and increase productivity, and can ensure that from one batch to the other batch you have the same quality,” he says.
“We are now collecting a lot of data from our processes, and the idea behind it is that we have a good, constant and reliable quality, and we can guarantee that we operate with the same quality worldwide. That’s the philosophy that is behind it. The same system and the same quality from all our sides, so that the customers, no matter where they are – whether they are multinational or local – get the same quality.”
While maintaining a consistent level of quality that has earned the company widespread trust, Perlen Packaging keeps a vigilant eye out for new materials and ways to improve current ones, in order to enhance its products.
We’re used to reacting to new challenges.
“That is a constant challenge, and a constant demand that we have with our suppliers,” Wolfgang affirms. “We expect our suppliers to look into things like stable economies and that they come up with new materials. We are also looking into new areas ourselves, where new materials are coming on the market and we try to evaluate how important those materials might be.”
The company has its own innovation teams conducting research and development into multilayer barrier materials. “We mix all the disciplines. We have applications, we have R&D, we have production and also sales, and then we develop that on a team level, we develop these new ideas,” Wolfgang enthuses.
“We have the spirit of continuous improvement in our team, and we are not afraid of challenging any new segments or any new requirements that may come from the market.” That includes growing demand, mostly in Europe, for sustainable and recyclable packaging.
“The circular economy is something we consider as a challenge, obviously, but also as a chance for us. That is something that’s coming up here in Europe,” he says. One way Perlen Packaging has reacted to this opportunity is to develop blister packs where each component is made of the same material.
“So far, the classic blister pack has two components: one is the bottom material, where you have the tablets, and then you seal the lid on top of it, normally with aluminium,” Wolfgang explains.
“We have now been able to develop a one-component blister package that has a PVC barrier lid, so the lid and the bottom material are the same component.” Perlen’s R&D teams are also working on developing halogen-free materials.
“It’s not just about addressing the circular economy; we are also working on new materials so that we can provide the market with alternatives,” he adds. Because of the nature of the industry, Perlen’s forward-looking mentality also requires patience – it takes a minimum of three to five years before a new innovation can materialise into new products.
“If you supply the pharmaceutical market, nothing is going to happen in a very short period of time because of all the approval procedures,” Wolfgang concedes. “Nevertheless, you have to monitor the market and be aware of what’s going on while trying to use new things which are coming on the market.”
The COVID-19 pandemic has shown that planning ahead isn’t always easy. But while Perlen Packaging is factoring in more than the usual amount of “uncertainties” for the coming year, Wolfgang is optimistic: “We’re used to reacting to new challenges, and we are still a very flexible organisation.”
Proudly supported by:
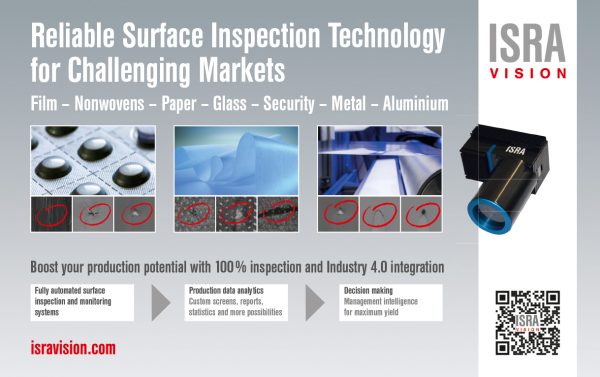
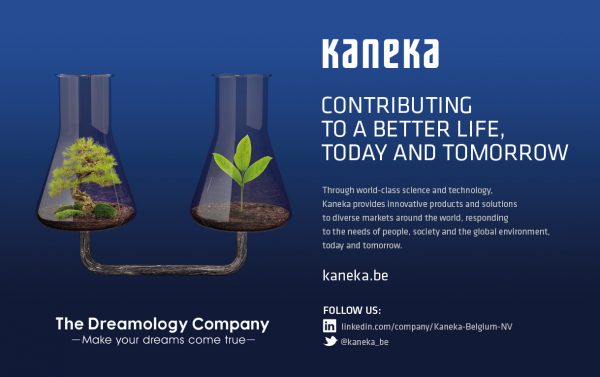
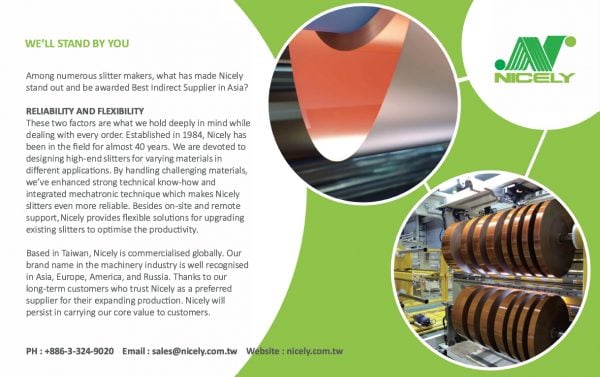
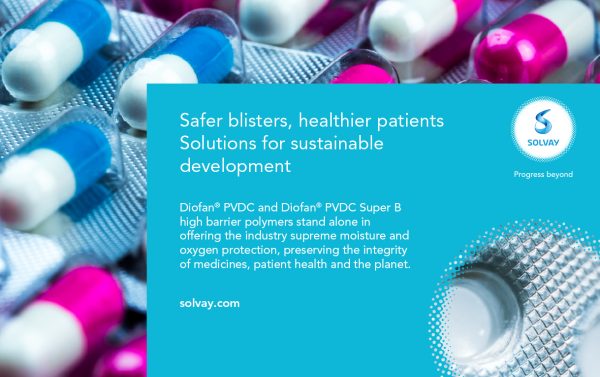
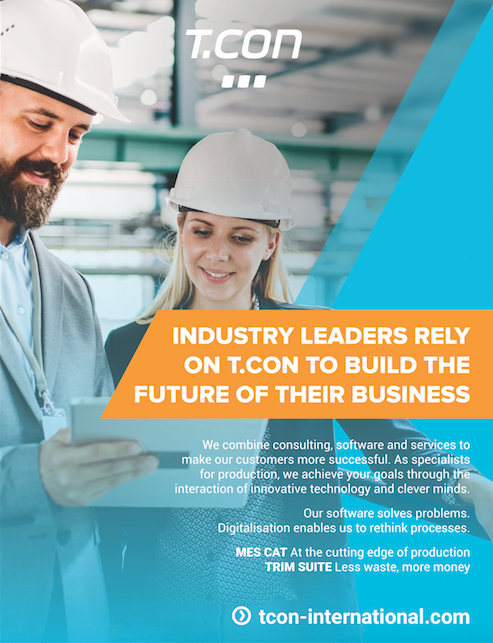
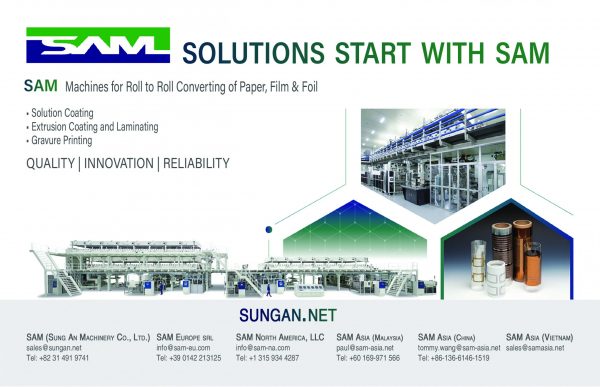