Having spent his entire working life in the packaging industry, spanning 29 years, Wolfgang Grimm is a firm believer that packaging design is just as important as the product itself. With experience in management positions across Germany and Switzerland at VAW Europack Export and Danisco Flexible Schüpbach, Wolfgang joined Perlen Converting at its Switzerland headquarters as Managing Director in 1998.
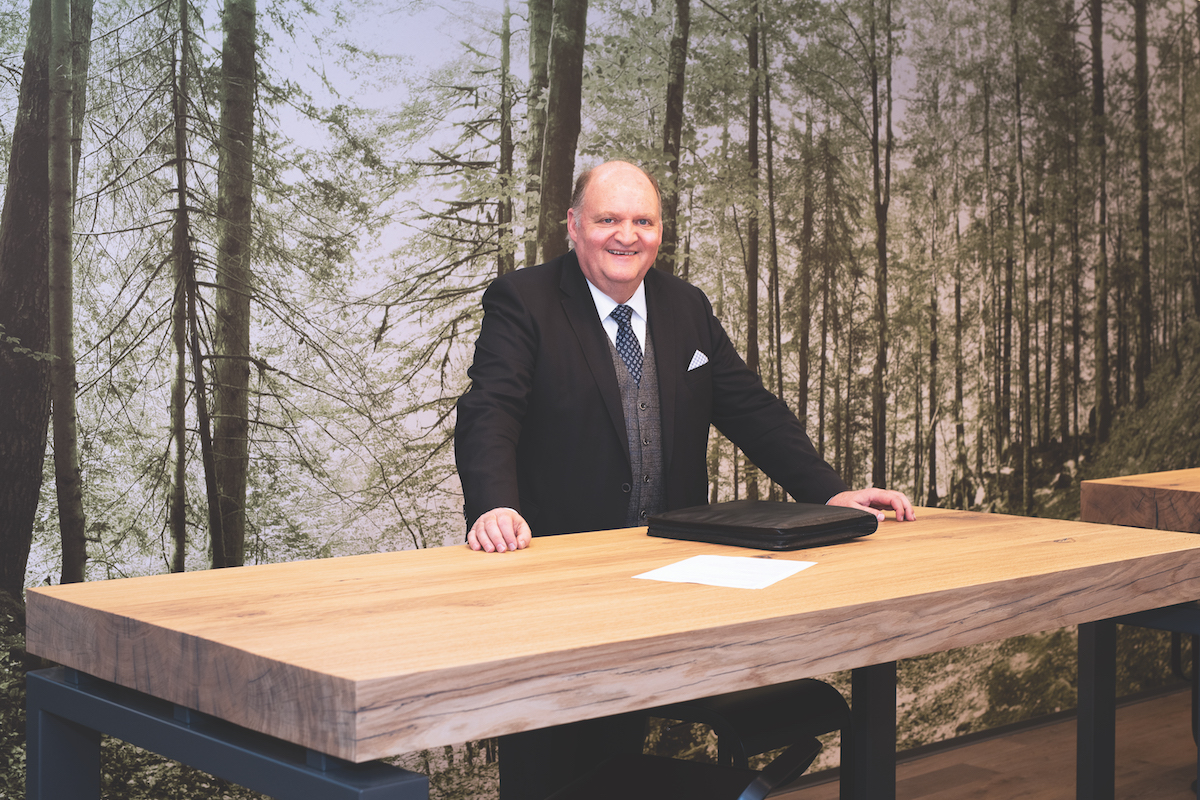
When its parent company, CPH Group, decided to restructure the organisation in 2003, Perlen was split into three divisions: packaging, paper and chemistry. Given his track record, Wolfgang took charge as CEO of its packaging division, Perlen Packaging, championing its vision to grow into a global packaging giant.
As the only system supplier providing film production and coating geared entirely to the needs of the global pharmaceutical industry, Perlen Packaging today has sites across Switzerland, Germany, the US, China and Brazil.
Following the opening of Perlen Converting LLC in 2005 in the US, the business then acquired a company called ac-Folien.
“This was a backward integration, as we already had the barrier pharma films. With ac-Folien we also then had the PVC mono film production in our portfolio,” Wolfgang explains. “It meant we could offer a complete range of products to our clients. The acquisition was a significant investment for us and entailed another €15 million to extend the capacity and infrastructure of the company to supply mono films for our barrier films and to the market.”
Global reach
Wolfgang says the business has been operating and expanding continuously with this model, growing from one to five production sites around the world. “Expanding our global presence is a step-by-step process. If you divide the pharmaceutical market into different geographical sections, you’ll notice that European markets are more saturated, with a growth rate of around 3%,” he notes.
“On the other hand, if you look at markets like Brazil, Asia, China and India, you’ll see double-digit growth rates of at least 10%. We operate globally so we have to adapt our strategy to suit each individual market.”
Perlen Packaging generated just under 20% of its net sales in Asia in 2016, which encouraged the business to open its own pharmaceutical film coating facility in Suzhou, China, that same year. Optimised to produce medium barrier blister films, the coating line is the largest and most technologically advanced PVdC coating line in Asia.
Core parts of the coating stations are a joint development between Perlen’s coating experts and the machine supplier’s engineering teams.
“We’re now in the process of upscaling and increasing the workload at this site and gaining the necessary licences from the China Food and Drug Administration so we can produce our products locally and distribute them throughout the country,” he explains.
“The Chinese government is focused on the pharmaceutical industry because it wants to achieve a global standard level within the Chinese domestic market, and it requires a high-quality range of packaging materials to store and export materials. This includes packaging for both liquid and powdered products.”
Tapping into the emerging Latin American pharmaceutical market, Perlen last year acquired a 60% majority share in Sekoya Indústria e Comércio of Brazil. In addition to its distribution activities, Sekoya also maintains its own finishing plant in Anápolis, Brazil, which tailors film products to the specific needs of the region’s pharmaceuticals customers, enabling Perlen Packaging to enhance its supplier flexibility and serve the Latin American market faster and more efficiently.
“We grew by around 20% last year, which means we’re growing faster than the market. This growth was largely supported by our leading position in the blister packaging market,” Wolfgang explains.
“We make high-barrier materials for packing pills, tablets and capsules and we’re now in a position to look into other sectors of the pharmaceutical market. Our aim is to deliver the same quality and flexibility to our global customers, no matter their size, as we have done in Europe.”
Perlen will continue to expand its European business but Wolfgang emphasises that the emerging markets will be the real catalysts for growth. “Our strategy is localised and twofold. First, we’ve followed our existing multinational customers into these markets, so we need to ensure we provide the same quality and services they’re used to.
By being on the ground, we enable them to grow their own businesses. Second, we’ll add to this offering by generating new business and forging new partnerships within the domestic pharmaceutical industry.”
To remain a quality leader in every product market, Perlen upholds the highest standards in its policies and operational processes. “As we grow internationally, our objective is to apply the same procedures, quality standards and GMP regulations as we have in Europe. It’s about worldwide standardised quality,” he remarks.
“At the same time, my credo is always one step ahead. We try to anticipate market swings and future trends so we’re able to react quicker than our competitors.”
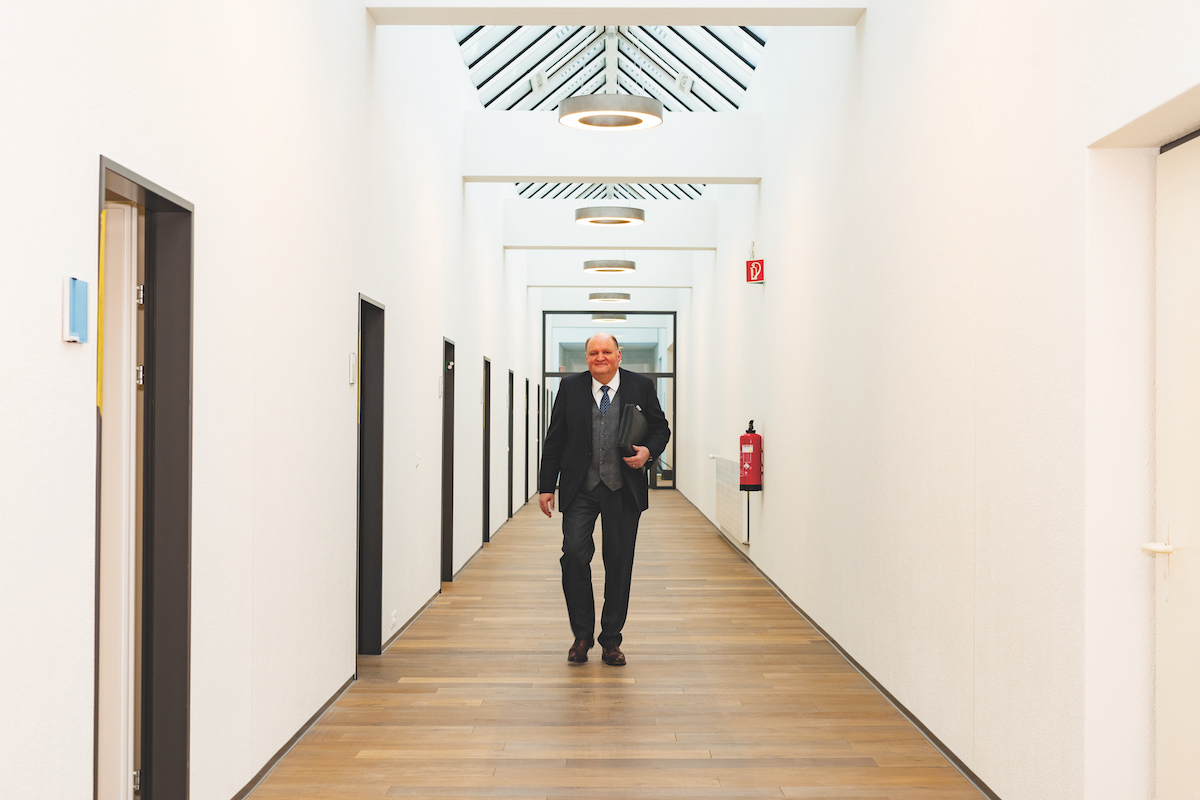
Inhaler innovation
For the first time since the invention of dry powder inhalation in 1959, Perlen Packaging revealed its PERLAMEDTM-BLISTair in 2017, the world’s first disposable single use inhaler. Consisting of two thermo-formed foils that enclose the active pharmaceutical ingredient, the device sets a new standard when it comes to simple design and low manufacturing costs.
“The packaging and the inhaler are one and the same, making this device a first in the global respiratory market,” Wolfgang says.
“Innovation like this gives us a distinct edge over our competitors – it’s revolutionary.” He insists that this technology will allow other pharmaceutical companies and customers to break into a market that was once blocked due to investment costs and the limited spending capacity of patients in emerging markets.
Its field of applications is wide, from asthma and vaccines to emergency and military applications and even pain and cold treatments. As a result, the device has won several awards including the German Packaging Award 2017, Best Drug Delivery Device in the CPhI Pharma Awards 2017 and Swiss Packaging Award 2018 and was named the World Packaging Organisation Worldstar Winner 2018.
“Innovative products like these initiate a new approach to the market. We’re not only supplying the packaging material to the pharmaceutical company or the contract packer, but we’re also authorising other companies in the packaging field,” Wolfgang points out.
“We’re cooperating with packaging machine suppliers and contract packers so that we are in a position to supply the finished device to the pharmaceutical market and the wider industry.”
Sustainable supply
By consistently aligning its processes, plants, products and the environment to the needs of the pharmaceutical industry, Perlen Packaging has attained the highest ISO qualifications. “It’s important that we comply with the highest quality energy, environment and hygiene standards – they are the basis and guarantor for the systematic and continual strengthening of our market position,” says Wolfgang.
“We are also committed to energy-efficient and environmentally sound production, which is encouraged by the definition of individual annual objectives.”
As a global leader in pharmaceutical packaging solutions, Perlen assumes a responsibility to play a positive role in the communities and environments in which it operates and serves. Wolfgang ensures that this commitment to quality and sustainability is consistent throughout the entire supply chain and Perlen works closely with its partners to improve their supply chain sustainability as well.
Through this proactive engagement, the business aims to promote innovation, manage performance and risk, and secure competitiveness while ensuring business continuity.
Today, Perlen Packaging has a worldwide sales network of more than 50 local partners, which represents the business across 85 countries. “As a global supplier, we always aim to give the same high standard of service and quality to our customers no matter where they are in the world,” he reasons.
“We’re audited by our customers and we regularly audit our suppliers to ensure they continue to meet our high standards. Every supplier we consider working with goes through a strict qualification process where we test the material and determine whether their business is scalable.”
Wolfgang encourages all suppliers to come forward with any new raw materials to create new products or improve existing ones. “Once a supplier has passed our tests and has been approved, we look to maintain a long-term relationship based on mutual trust and collaboration,” he says. “The reason we’re so tough during this process is because we’re responsible for what we deliver to our customers and we only want to deliver the best.”
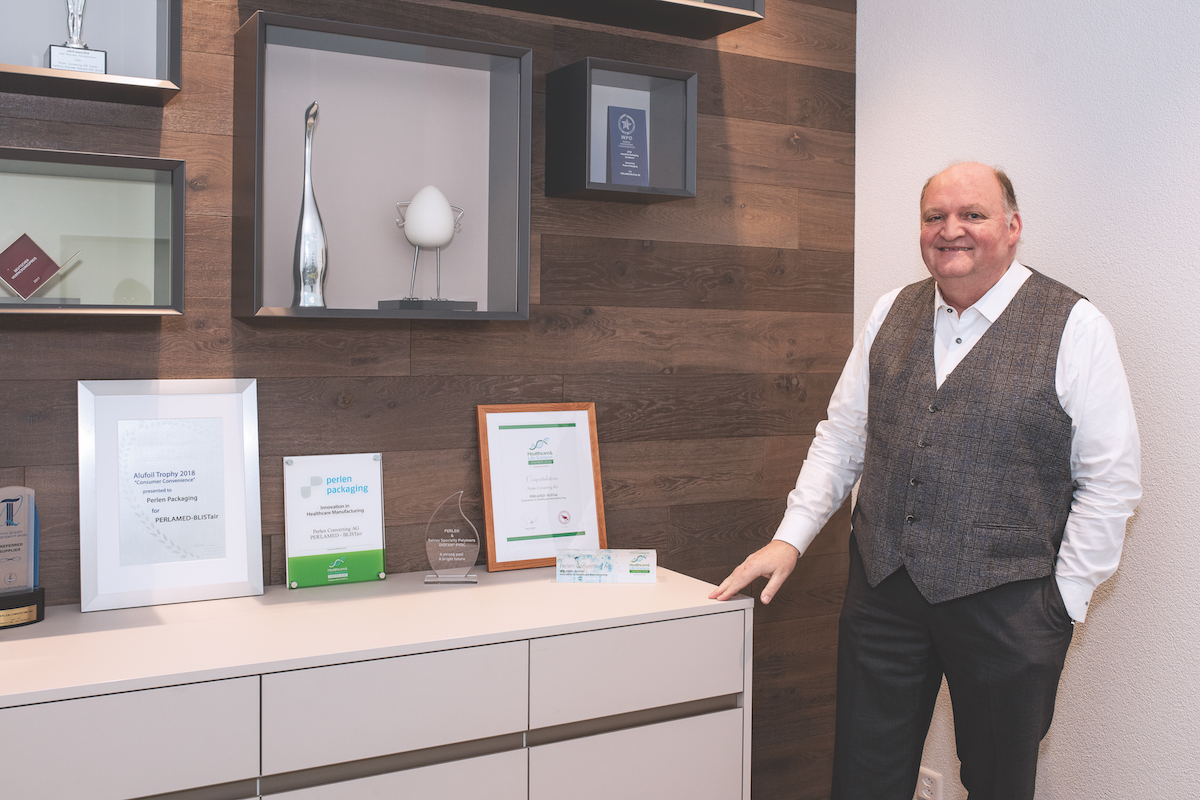
Innovating for the future
It is Wolfgang’s intention to bring Perlen’s packaging business to over CHF200 million (€176 million) turnover within the next few years.“Our new Asian and Brazilian operations are a step in that direction. Pharma is our key market, and we will remain focused on it, but we are also pushing for new developments in blister packaging that can be used across a range of sectors.
We are always redeveloping our products to see where our packaging systems and solutions can be applied in other markets.”
However, Wolfgang realises that this cannot be done alone. “We are taking advantage of some new opportunities to collaborate with other companies in the packaging field while also assisting the pharmaceutical companies in developing new products,” he notes. “We were only able to develop our inhaler innovation because of the advanced technology we’ve used in high-barrier products and blister packs.
“One innovation leads to another. We look to add increased flexibility into our processes to respond to industry demands. We’re very focused on adapting to Industry 4.0 and we’re looking to apply automation in all areas to increase efficiency and replicability,” Wolfgang insists.
“Our ERP systems are continuously upgraded and we have just introduced the latest SAP S/4HANA. If we want to be a quality leader, we have to be a technology leader first and this applies to our manufacturers and equipment suppliers also.”