All industries face regulatory guidelines and legislation to improve their sustainability.
With renewables expected to play a critical role in the global transition to a clean energy future, the world needs mining more than ever to meet 2050 net zero goals.
To build cleaner energy solutions such as solar, wind and water energy, the mining industry will need to mine six times more metals than today.
As the International Energy Authority notes, an energy system powered by clean energy technologies differs profoundly from one fueled by traditional hydrocarbon resources.
A triple challenge
Solar photovoltaic plants, wind farms and EVs generally require more minerals to build than their fossil fuel-based counterparts.
Extracting these minerals under new sustainability requirements is challenging. From July 2023, under Net Zero Australia, the Australian Safeguard Mechanism has set a hard CO2 baseline requiring sites to reduce their emissions by 4.9 percent per year to reach a 30 percent reduction target by 2030.
Mining companies themselves have made commitments to cut emissions by 50 percent and reach net zero over the next 10–20 years.
As the International Energy Authority notes, an energy system powered by clean energy technologies differs profoundly from one fueled by traditional hydrocarbon resources.
Mining operators therefore face a triple challenge. They’re already one of the world’s prominent carbon generators but must increase output while also achieving their own decarbonization objectives.
There are various approaches to decarbonizing mining, from using energy-efficient equipment to low carbon-embracing technology to improve operations.
The challenge of decarbonizing the mining industry is substantial, particularly as several critical processes are notoriously difficult to abate.
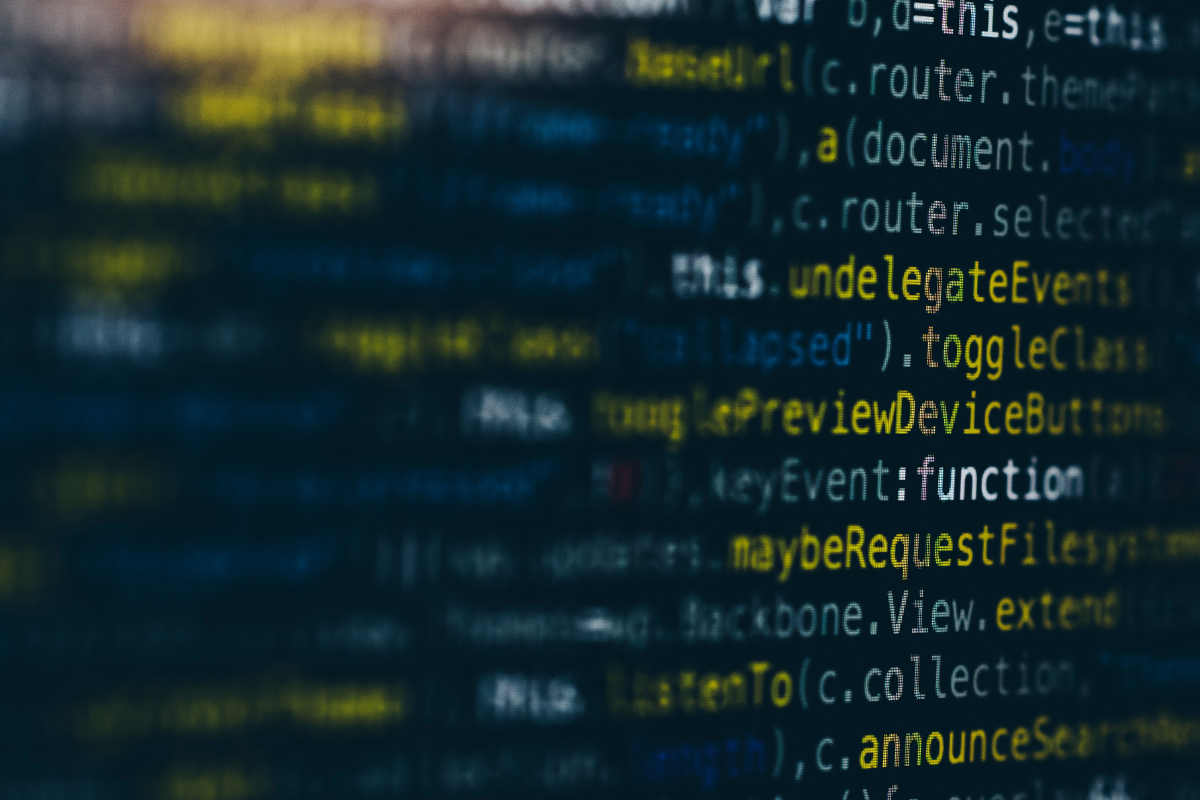
Decarbonizing with data and analytics
A key contributor to mining’s emissions is diesel equipment. The average mine site, with a fleet size of approximately 40 trucks, currently contributes 150,000 metric tons of carbon per year from diesel equipment.
In total, the mining sector’s heavy-duty trucks and excavators alone account for six percent of Australia’s total energy consumption. However, presently, there are no zero or even low-emission machines in commercial operation.
Many operators believe the pathway to haul fleet decarbonization will be via battery or hydrogen equipment options.
But these technologies are yet to be proven, developed, commercialized and built at scale. There’s a clear risk these technologies will run late: they’re unlikely to be available at scale before 2030.
One option that could make a significant difference is using data to improve productivity and efficiency.
The availability of more granular data presents an opportunity to precisely measure and enhance mining operations, realizing productivity levels similar to those that digitization has delivered in other industries.
For example, with mining vehicles, data and analytics (DnA) can be used to maximize payloads, reduce idle time, off-haul or wasted operation and enable more efficient driving.
For example, with mining vehicles, data and analytics (DnA) can be used to maximize payloads, reduce idle time, off-haul or wasted operation and enable more efficient driving.
By pulling all sensor data at high frequency from all the major mobile equipment manufacturers, MaxMine has accrued over 10 million hours of mining operational data.
Similar to the feedback a race driver receives from their laps, this information is applied to each mining equipment operator: from the best gears to the best speed for each section of road they travel on.
Through leveraging this and other MaxMine data, such as Asset Health, the average open pit mine could reduce its carbon Scope 1 footprint by up to 20 percent. This means a mine could reduce its carbon footprint by about 30,000 metric tons of CO2 – equivalent to over 800 hectares of forests preserved in one year.
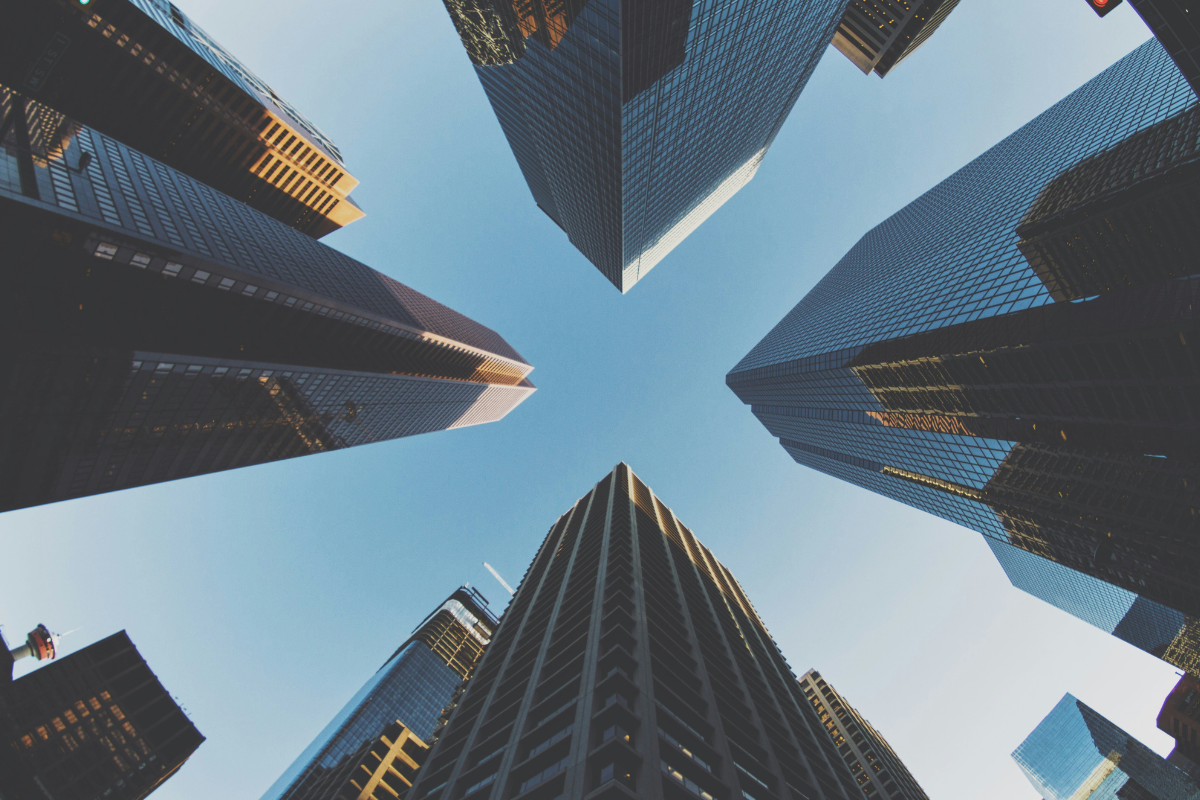
Bringing sustainability to the boardroom
The sustainability conversation, along with the data and analytics strategy required to enable it, needs to start in the boardroom.
For mining, sustainability means ensuring long-term business viability, addressing regulatory compliance and reputational risk, meeting stakeholder and societal expectations and encouraging innovation. It is core and fundamental to business strategy and directly impacts the bottom line.
Nickel, for example, is currently experiencing skyrocketing demand and prices due to its use in EVs. Alongside this is the increased pressure for environmentally sustainable, low-carbon supply chains, while many costs, such as fuel costs, are rising.
In some jurisdictions, carbon liabilities are emerging as well. McKinsey estimates that through implementing DnA-enabled practices, fuel costs per unit of production could be reduced by up to 20 percent through operational improvements.
Another area where DnA can play a role is in improving operational safety by objectively assessing risks and informing effective countermeasures.
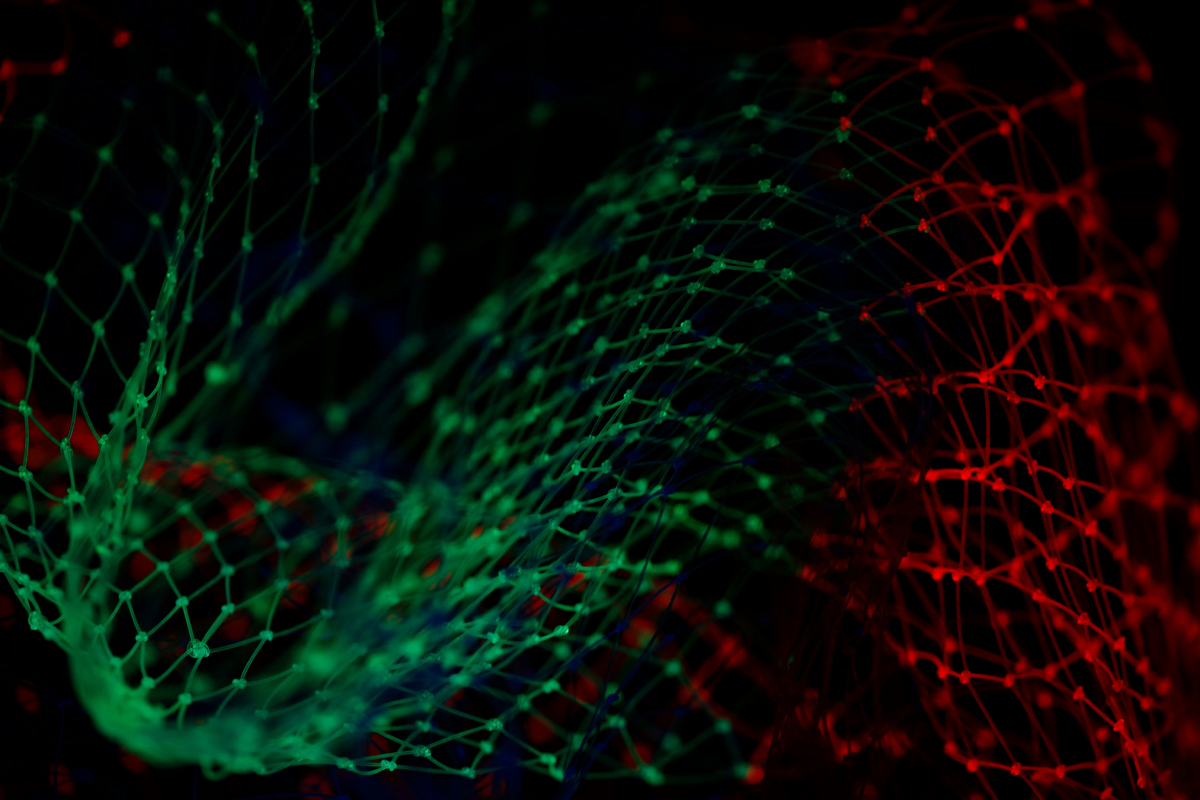
Already making progress
Great strides are already being made in using data and analytics to improve sustainability in mining.
NRW Civil & Mining (NRW), one of Australia’s leading contractors, wanted to reduce greenhouse gas emissions at the Karara Iron Ore project in Western Australia.
A key area of focus for this was enhancing operator behavior in the truck fleet, ensuring optimal travel speeds to maximize safety and productivity while reducing road degradation and the overall carbon footprint of its operations.
Using the MaxMine platform, NRW collected highly granular data about all its mobile mining equipment in operation. Working with data scientists, they were able to generate insights that provided personalized performance feedback to drivers.
Having more comprehensive, accurate and relevant data gives mine site operators the confidence to make significant operational decisions that target carbon emission reduction.
This has resulted in a range of efficiencies, such as reduced fuel consumption, minimized tire wear and an average fill factor improvement of three extra metric tons per load. This translates to an additional 612,000 metric tons of material being moved annually without incurring any extra costs.
Having more comprehensive, accurate and relevant data gives mine site operators the confidence to make significant operational decisions that target carbon emission reduction.
This translates into not just economic benefits but also positive environmental changes and progress toward sustainability targets.
The world needs mining to supply the net zero transient. However, the industry also needs to improve its productivity and efficiency. Leveraging data can make mining safer and more efficient and accelerate the sustainability of humanity’s scarce resources.